These have optimised stress distribution and deformations are contained without affecting the flatness of the mould coupling surfaces. The bench cross-member parallelism control system verifies possible loading errors, in which case the pressing cycle is promptly stopped.
All phases of the press cycle are controlled by proportional reaction valves which ensure high precision and a wide range of adjustment. Oil consumption is optimised during the low pressure pressing cycle by the flow rate multiplier, allowing for considerable energy savings. The new hydraulic circuit delivers a greater number of cycles, high precision and repeatability of the various phases of the cycle. Maintenance procedures are facilitated by the use of high quality components and elimination of a number of flexible hoses.

The ejector system with four thrust points (using hydraulic cylinders synchronised and controlled by proportional valves) ensures that the punches are kept flat during the extraction phase. This guarantees a longer lifetime of mould wear parts. The automatic mould coupling device is integrated into the thrusting cylinders.
The new hydraulic power unit reduces electrical power consumption by utilising a pump with variable capacity that only absorbs the power actually required by the circuit. This avoids oil overheating and improves cooling. The loading carriage is driven by a brushless motor and linear guide.
A shutter type hopper with a controlled opening and closing system is used to regulate the powder dispensing cycle in the grid without taking time away from the complete press cycle. The electronic control panel is used to set all the adjustment parameters of the press and the powder loading carriage, display the press operating parameters (including in the form of graphs) and save the recipes and the operating parameters. It also provides a historical list of the alarms and the modifications made to the parameters.
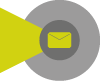
Did you find this article useful?
Join the CWW community to receive the most important news from the global ceramic industry every two weeks
Recent articles
Gruppo B&T at Ceramics China 2025
Jun 30, 2025
Cersaie 2025 already booked out
Jun 27, 2025
GMM USA installs IMAnalytics system in the USA
Jun 26, 2025