Bongioanni partner of Wienerberger for the new Kanjiža plant
The new production plant in Kanjiža, northern Serbia, will double the production capacity to 4.2 million square metres of roof tiles/year.
In March 2022, Wienerberger completed yet another investment involving the modernisation of its roof tile production plant in Kanjiža, northern Serbia. The €19 million project focused on completely upgrading the existing plants with state-of-the-art technology that will not only double the production capacity to 4.2 million square metres of roof tiles/year but will also expand the range with extremely high-quality large-size premium products.
Amid strong growth of the construction sector in Serbia, the increase in production will enable the company to meet higher domestic demand and expand its exports to Montenegro, Bosnia, North Macedonia, Bulgaria and Albania.
The new products stand out for their modern and attractive design combined with rapid assembly due to their larger size.
Sustainability and safety played a key role in the choice of plants. The production site meets the highest standards of energy efficiency and utilises ergonomic, low-risk processes that safeguard workers.
The Kanjiža factory is one of the largest roof tile facilities in south-eastern Europe. Formerly known as Potisje Kanjiza, the company was acquired in 2018 by the Austrian giant, which changed its name to Wienerberger doo Kanjiza.
Bongioanni Macchine and its moulds division commissioned to supply forming equipment
Wienerberger doo Kanjiza chose Bongioanni Macchine spa’s Moulds Division to upgrade the roof tile line with suitable technology for the production of large size tiles. The two existing double mould presses were therefore upgraded and made suitable for the production of two standard tile types (Continental 9 and Twist 9) designed by Bongioanni Stampi in close cooperation with the customer. During development of the design, the company carried out checks on all couplings the tiles undergo during the production cycle (setting on the drying trays and on the H-cassettes, couplings for stacking and transport) as well as the roof installation check to verify that the roof tiles are perfectly weather resistant.
The project also took account of the possibility of producing previous models in smaller sizes, so further studies were carried out to ensure that all new and existing moulds could be mounted on the presses and Bongioanni Macchine’s technical department performed 3D simulations of the moulding process. This resulted in the installation of dedicated, purpose-designed equipment.
Bongioanni also supplied the moulds for all the accessories necessary for a high-quality roofing product (start glatki ridge tile, end ridge tile, ventilation tile, half twist tile, right and left gables).
On the main forming line, Bongioanni Macchine updated the mechanical part of the two 13PV-G presses (particularly the one subject to greatest wear) and adapted the machines to be able to hold the larger moulds. For this purpose, the bat loading line was modified and equipped with a single-blade, overlapping double-strand TGLDS type cutter complete with electric control panel featuring latest-generation SEW technology. Two automatic AC8P type bat loaders were also installed, each with eight mats, with launchers suitable for use with inverters for load speed optimisation equipped with double storage and pneumatically operated deviation.
These modifications were necessary in order to use larger clay bats suitable for the new models while at the same time optimising raw material consumption and energy usage.
The success of the project was due to the teamwork between Bongioanni’s technical and production departments, which together managed to meet each individual request and achieve the objectives within an extremely short timeframe. Bongioanni also wishes to thank the Wienerberger Kanijza team for their collaboration, particularly the project managers R. Reckeki, A. Pietrzak and L. Sanders.
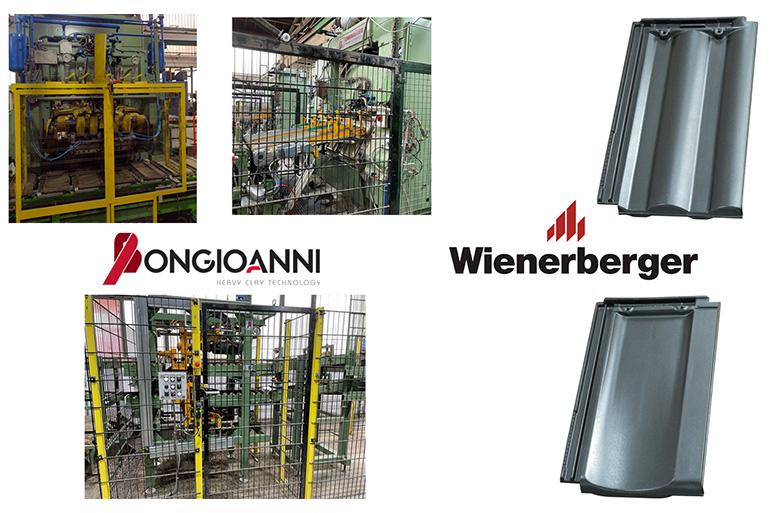
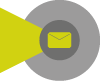
Did you find this article useful?
Join the CWW community to receive the most important news from the global ceramic industry every two weeks