Cimes automates traditional deburring systems
At the recent Tecna 2024, (Rimini, 24-27 September) Cimes presented the world’s first deburring machine capable of continuously cleaning all four sides of ceramic tiles and slabs, thereby fulfilling the growing global need to automate traditional deburring systems.
The system offered by Cimes ensures linear tile and slab movement without the need for rotation, an extremely critical operation for unfired tiles and especially large-size slabs. This in turn guarantees a higher percentage of first-choice finished products. Eliminating all stoppages and ensuring continuous production also increases production capacity.
The software also enables the machine to self-adapt to slabs and tiles during production, thus avoiding the need to centre or guide products with the constant risk of breakage or damage. It will no longer be necessary to change the production line in the event of a size change.
But what makes this internationally patented system unique is the ability of the deburring heads to adapt to the angle and position of the tile or slab, unlike current systems in which the ceramic tile surface has to be guided towards the deburring head.
The angle and position of the tile or slab is detected by photoelectric sensors and sent to the PLC, which continuously calculates and corrects the position of the heads prior to deburring.
This improves production flexibility, especially in the size change phase, because it is no longer necessary to alter the entire deburring area as is currently the case. All the operator has to do is set the size undergoing production from the Industry 4.0-compatible touch interface, after which the deburring operation will be performed fully automatically.
With this innovative design, it is possible to perform complete deburring of the tile or slab in a space of just 5 metres instead of the 10-12 metres required with traditional systems, a result that was unthinkable until a few months ago.
Its compact size and extremely high level of versatility (with a wide range of different types of tools) enables the machine to be installed in multiple positions along the production line. For example, it can be positioned at the dryer exit for cleaning the lower pressing burr (increasingly necessary in modern continuous pressing systems), or at the end of the line for cleaning the edges after traditional and/or digital glaze applications.
In addition to the obvious advantage of making the lines more compact and versatile, the use of a single machine reduces maintenance costs and brings unprecedented production flexibility.
The Cimes deburring machine is a scalable and modular system on which deburring heads can be added or removed with ease. It also adapts to any feed width.
In view of these advantages, a number of large ceramic groups around the world have shown strong interest in this new technology, which has already been adopted in a number of facilities.
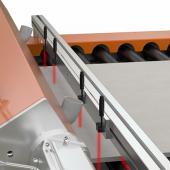
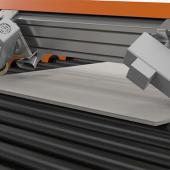

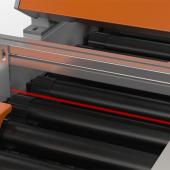
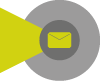
Did you find this article useful?
Join the CWW community to receive the most important news from the global ceramic industry every two weeks