Continuous inkjet pumps: the next generation of printing systems
With the new generation of KNF Smooth Flow pumps, all pumping operations in a CIJ system can be performed by diaphragm pumps.
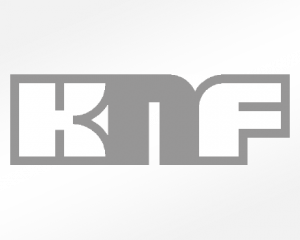
Continuous inkjet (CIJ) systems print information such as expiration dates, serial numbers and batch codes on a range of surfaces such as cardboard, plastic, glass and metal in many industries worldwide. Various types of pumps can be used for this important task. In the past, these were often a combination of gear pumps and diaphragm pumps.
But thanks to the enormous progress made in diaphragm pump technology, first and foremost the very low pulsation levels, diaphragm pumps can now be used in all CIJ system applications, where they bring many economic and technical benefits.
The operation of CIJ systems is based on a number of different pumps. As shown in figure 1, ink is normally transferred from a large container (1) to a reservoir (3) via a dispensing pump (2). From here, the ink is transferred to the printhead (6) via a pressure pump (4). A damper (5) is used between the pressure pump (4) and the printhead (6) to reduce pulsation. In the printhead, ink flows through the nozzle (7) creating a continuous series of small ink droplets that can be individually charged. The charged droplets are then deflected through the electrodes (8) and impinge on the object to be printed (9). The uncharged droplets fly in a straight line into the gutter (10) from where the ink is recirculated into the reservoir (3) via a gutter pump (11). To prevent the ink from drying out and consequently damaging the system when it is turned off, continuous inkjet systems are also equipped with a solvent pump (12) which delivers solvent to the nozzle to free it of ink residue.
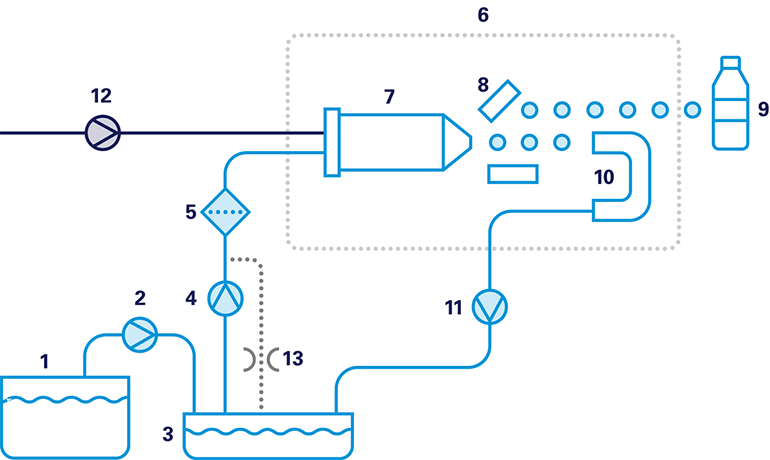
Disadvantages of gear pumps in CIJ systems
In the past, many of the pumps adopted in continuous inkjet systems were gear pumps because they produced less pulsation than diaphragm pumps. This has changed dramatically in recent years when KNF pushed back the limits of its unique Smooth Flow technology. Modern KNF liquid diaphragm pumps can operate at very low pulsation levels, which means that the bypass and damper can often be eliminated, allowing the entire printing system to be significantly simplified.
Most gear pumps give rise to cavitation that may damage inks and generate bubbles in the ink. In addition, their self-priming capability is inferior to that of diaphragm pumps and most gear pumps are not entirely safe for dry operation, not to mention the fact that gear pumps pose a risk of polluting the ink with particles produced by gear abrasion.
Diaphragm pumps. The future of continuous inkjet systems
With the new generation of KNF Smooth Flow pumps, all pumping operations in a CIJ system can be performed by diaphragm pumps. When this pump is used as a pressure pump (4), the orifice bypass (13) becomes obsolete due to the Smooth Flow pump’s superior controllability and low pulsation. Depending on the specific system design, the damper (5) may also become obsolete. This reduces the complexity of the system and saves costs.
For all other pumping operations, many CIJ system manufacturers already adopt diaphragm pumps due to their superior characteristics. They are self-priming, can run dry safely and produce almost no cavitation. They are also extremely robust and offer long life and low maintenance. Finally, their cleanliness and resistance to chemicals are further significant advantages.
The Smooth Flow range consists of the FP 70, FP 150, FP 1.150, FP 400, FP 1.400, FK 1100 and FK 1.1100 series.
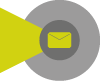
Did you find this article useful?
Join the CWW community to receive the most important news from the global ceramic industry every two weeks