A green revolution in the digital glazing of ceramic substrates
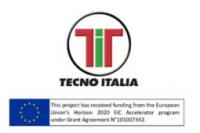
TECNO ITALIA presents DigiGlaze 4.0, an innovative glazing technology that uses traditional completely water-based glazes and Drop on Demand (DOD) technology, and that is capable of permanently resolving the problem of workplace pollution caused by silica and toxic vapours
by Alex Elmetti, Andrea Palladini, Dino N. Boccaccini (Tecno Italia)
Building on its twenty years of experience in the construction of machinery for the ceramic tile industry, TECNO ITALIA has reached another milestone: developing an innovative glazing technology capable of permanently resolving the problem of workplace pollution caused by silica and toxic vapours, a frequent occurrence on traditional spray glazing lines.
The project, which took about four years and has already resulted in seven international patents, led to the development of DigiGlaze 4.0, a digital printer for glazing ceramic substrates that uses traditional completely water-based glazes and Drop on Demand (DOD) technology.
Tested since January 2019 at Antica Ceramica di Rubiera industrial plant in the Sassuolo ceramic district, DigiGlaze 4.0 is now a fully-fledged green technology for ceramic tile production. In recognition of its value in terms of environmental sustainability, the Glazetile project (www.glazetile.eu) received funding from the European Union’s Horizon 2020 EIC (European Innovation Council) Accelerator programme, as well as being awarded a Seal of Excellence by the European Commission for its focus on occupational health.
DigiGlaze 4.0: Glazing with 100% water-based glazes
DigiGlaze 4.0 solves the problems associated with current technologies and aims to transform the digital glazing of ceramic substrates. One of its main strengths is the use of traditional glazes and additives, which are completely water-based (dry additive percentage <0.5%, viscosity of 11-15 sec. and density of 1,350- 1,500 g/l) and have a standard particle size (50μm) with no need for further milling. All types of glazes, engobes and “smaltobbio” (a highly vitrified engobe) can be used, whether white or coloured, as well as glues. In addition, the printer can also be used to apply protective glazes on products to be polished, lapped or left natural.
In terms of the product’s aesthetic quality, DigiGlaze 4.0 creates smoother and softer surfaces due to the lower level of roughness and superior application quality, while the higher white point means that all colours are more intense and luminous, increasing the sense of depth and contrast in the designs.
The benefits in terms of environmental sustainability are obvious. Compared to traditional technologies, DigiGlaze 4.0 eliminates both dust and harmful emissions during the firing process, reduces water consumption for automatic washing and, most importantly, reduces glaze wastage by up to 30%. It also completely eliminates the need for extraction equipment or booths in the glazing process as no harmful substances are released into the working environment.
As for its operation, the DigiGlaze 4.0 is installed at the point where the double-disc, curtain coater, airless or bell-shaped applicators are normally located and no substantial changes need to be made to the glazing line apart from disconnecting the extraction system which is no longer required. No change in the temperature at the dryer exit is necessary for correct operation, although the decision may be taken to lower it from the usual temperature depending on the product. The printer uses proprietary and patented DOD technology to control the discharge rate and application rate, with the option of programming drop size and frequency from the control panel. DigiGlaze 4.0 operates only when a tile passes through and applies glaze according to the tile’s real size, eliminating the normal wastage caused by oversized work. The machine reaches a production speed of up to 65 m/min with glaze deposition of 20 to 100 g (on a 30x30 cm size) and encounters no problems with sedimentation or nozzle clogging.
7 DIGIGLAZE 4.0 for Cersanit Group
After a few months of testing and production, the Cersanit Group of Kielce, Poland, confirms the outstanding performances of DigiGlaze 4.0 technology, by purchasing 7 new machines to be installed in its factories in Opoczno, Wałbrzych and in the production plant located in Ukraine.
The reasons that convinced the Cersanit Group to take this decision have to be found in the concrete results and performances obtained thanks to DigiGlaze 4.0, an exceptionally convenient and innovative green technology designed for the glazing process.
READ THE FULL ARTICLE IN CERAMIC WORLD REVIEW No. 141
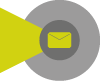
Did you find this article useful?
Join the CWW community to receive the most important news from the global ceramic industry every two weeks