The Industry 4.0 transformation begins with strategies
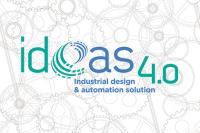
Enrico Amodio, Pietro Cassani - Ideas 4.0
As the perfect combination of digitalisation and production process automation, Industry 4.0 represents an epochal transition. What is now known as “the fourth industrial revolution” is sweeping through the world of manufacturing, driven by changes in technology.
“Big data” and advanced analyses, the Internet of Things (IoT), automation, robotics and artificial intelligence are ushering in a scenario of distributed innovation that will increasingly accompany the evolution of processes towards maximum efficiency based on interconnection of the entire factory. The challenge is no longer limited to the availability of individual 4.0 machines or advanced CRM solutions that have been around for years.
It would likewise be a mistake to think that Industry 4.0 merely involves introducing additional levels of automation to production lines. If change is the keyword, a correct approach to the concept of “smart manufacturing” must begin with a change of business model and strategic vision, which in turn depends on technological expertise.
A proper analysis of the opportunities offered by technology is key to the process review that will enable us to achieve more efficient processes (with clear economic benefits), improved customer service and production innovation.
The issue is often addressed by focusing on just one of these goals, for example increasing efficiency and productivity, and then discovering that the opportunities deriving from the digitalisation of processes and the automation typical of a smart factory have the direct consequence of improving the level of service offered to the market. In other words, the advantages obtained by implementing a factory 4.0 are never unidirectional but have an impact on the business’s value chain.
It is for precisely this reason that the path towards Industry 4.0 requires the change in business model and strategic vision we mentioned above. The potential points of arrival are plain to see in our daily lives: from the diffusion of virtual banks to the revolution in transport systems in large cities, from retail (the first fully-automated supermarket is already in existence) to the world of machinery (packaging is a good example).
- Virtualisation and digitalisation
A combination of innovative production technologies, sensors and monitoring and analysis instruments enables companies to control complex issues.
Virtualisation consists of the ability to use specific software to simulate all internal processes so as to minimise unknowns, reduce production and set-up times and monitor the level of efficiency of the factory, from real-time cost generation to changes in production processes and benefit or defect analysis.
This is already a reality in many industrial sectors. An example in the food industry is that of Ferrero, which develops its lines at a virtual level prior to production. At higher levels it is also possible to simulate the company’s potential development.
A supervision system of this kind can clearly also be implemented in the ceramic industry, which brings clear advantages in terms of knowledge of production processes and of the bottlenecks that occasionally arise at various points in the production cycle (preparation, kiln, packaging, etc.).
The first step is to gain a better understanding of one’s own production process. The software that interconnects the individual machines and collect the data that they generate is the driver of growth towards Industry 4.0. The second step consists of data analysis by the competent departments, without which the data would be entirely useless.
For example, a predictive maintenance system requires data processed by production technicians and by after-sales and customer service managers.
Real-time monitoring of production and sales performance is another major opportunity offered by today’s technology, but is beneficial only if it leads to initiatives for cutting costs or increasing sales volumes. This brings us to the issue of human skills and technical training. This is probably the first gap that needs to be filled in a recently initiated process that is bound to evolve rapidly in the future if we want to avoid the risk of having robots in the factory that no one is capable of handling.
This inevitably means progressing from digital technologies to organization and ultimately company strategies.
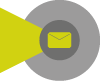
Did you find this article useful?
Join the CWW community to receive the most important news from the global ceramic industry every two weeks