Inter Ser presents Roll-X
ROLL-X is a new engobe applicator specially designed for coating the underside of tiles and slabs in thicknesses ranging from 3 to 20 mm.
With the growing trend towards the production of large ceramic surfaces, the application of refractory engobe has become a crucial step in the manufacturing process. Uniform application of engobe on the underside of tiles and slabs is now essential to protect the rollers and ensure the physical integrity of the finished products.
Building on the successful results achieved with Roll-X for small to medium-sized tiles, Inter Ser has developed the same machine concept for production lines dedicated to medium to large sizes.
ROLL-X is a new engobe applicator specially designed for coating the underside of tiles and slabs in thicknesses ranging from 3 to 20 mm. It is equipped with a 145 mm diameter silicone roller, laser-engraved to meet individual customer requirements. This allows for precise printing of logos, texts or markings and ensures consistent application, even on particularly smooth or irregular back patterns.
Easy to install on both new and existing production lines, Roll-X’s compact dimensions eliminate the need to split up or modify the existing line structure.
The following are the main advantages of using ROLL-X:
- Uniform and precise engobe application: the operator does not need to adjust the quantity of applied product, so it is no longer necessary to correct for differences between shifts.
- Elimination of refractory droplets and speckling defects on the surface thanks to the engraved silicone roller application process.
- Superior flatness as viewed by reflection, especially in the case of glossy surfaces.
- Possibility of printing logos or “Made in” lettering by means of laser engraving.
- The kiln rollers remain clean for longer, resulting in fewer stops for cleaning, which can be planned in advance and synchronised with other line stoppage activities. This increases the number of hours the kiln is full per month and reduces overheads and maintenance costs.
- The movement of the tiles inside the kiln is also improved, as is the efficiency of the kiln unloading machine. The operator consequently has more time to devote to other tasks and less manual unloading work, resulting in fewer defects and improved overall safety.
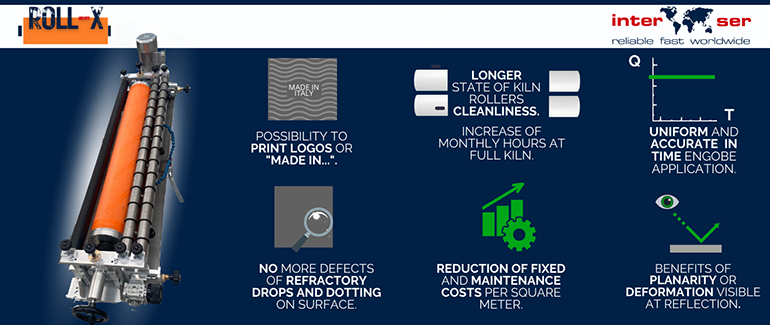
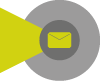
Did you find this article useful?
Join the CWW community to receive the most important news from the global ceramic industry every two weeks