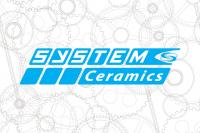
Unveiled at the System Ceramics Open House in late September, Superfast is the world’s first and only mouldless press for the ceramic tile industry, a process innovation with advantages and levels of performance that simply cannot be matched with traditional pressing systems. In particular, it allows ceramic companies to perform the entire production process with unprecedented flexibility and zero waste.
With its mouldless operation and unique belt system, Superfast is able to produce all conventional sizes based on 60 cm, 80 cm and 90 cm modules in thicknesses ranging from 3 mm to 30 mm, making the size and thickness change operation extremely quick and simple via software.
In addition to its simplicity, flexibility and ease of use, another major benefit of this new technology is the system for recovering ceramic waste originating from the pressing and pre-fire cutting stage. Thanks to a shaping process based on the double filling technique, 100% of the waste can be recovered and reintroduced into the production cycle after undergoing real-time grinding alongside the press and subsequent mixing ready for reuse. In the double filling operation, the recycled material is used to form the base of the ceramic tile and the pure spray-dried material is applied on top of this layer.
This extremely efficient and value-added process is managed easily by software, resulting in zero waste and consequently lower consumption of raw materials. Laboratory and industrial tests performed by accredited and independent research centres have shown that the aesthetic and technical quality of the finished tiles is identical to those produced using solely pure spray-dried powder.
In keeping with System Ceramics’ philosophy of developing cutting-edge technologies for increasingly sustainable manufacturing, Superfast is not just part of a circular production process with lower costs but also allows for up to 70% lower energy consumption than with conventional presses.
The process also stands out for its high productivity given that the Superfast press can achieve a daily output of 20,000 sq.m of tiles, a volume that would require the use of two conventional presses. Another advantage is the ability to work with any kind of spray-dried powder (porcelain stoneware, monoporosa, red body or dry granulate). While Superfast is designed to promote sustainable industrial development with a special focus on cutting costs and reducing the use of raw materials, at the same time the new technology is part of an innovative production concept focused on customisation and just-in-time manufacturing. These advantages have already attracted strong interest both internationally and in Italy, where major installations are planned from early 2020 onwards.
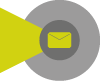
Did you find this article useful?
Join the CWW community to receive the most important news from the global ceramic industry every two weeks