Multi-spindle cutting lines for ceramic slabs
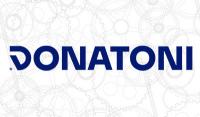
Donatoni Macchine has developed a new patented cutting system capable of cutting 1-2 cm thick slabs in a single pass, doubling the productivity of a traditional cutting system.
Donatoni, an Italian company based in Sant'Ambrogio di Valpolicella (Verona), has been developing slab cutting and floor and wall tile machining technologies for many years now and offers a number of solutions and patented systems for optimising these operations and allowing customers to increase their production capacity.
The solution that delivers the highest levels of performance is without question the Donatoni SX-5Q, a high-output cutting line used principally for machining marble, stone, sintered material and ceramic floor and wall tiles.
The line is managed automatically by the proprietary Parametrix software. The production process is integrated with a series of automatic loading systems and manual and robotic unloading and palletising systems, which distribute the products of various sizes to the different packaging bays.
The heart of the Donatoni SX-5Q cutting line is the rotary headstock with five independent spindles. This integrated technology system allows different sizes to be produced from a single slab in such a way as to optimise operation and minimise waste. Operational flexibility and cutting speed are the key features of the system and ensure high levels of performance.
Donatoni’s R&D department has worked hard to further improve this technology in response to growing demand for solutions for cutting and machining ceramic materials.
An in-depth study of the materials and the various production requirements has led to the development of the Donatoni HS-X5Q, a new patented cutting system equipped with a headstock with 5 completely redesigned cutting heads capable of cutting 1-2 cm thick slabs in a single pass. The productivity of this solution is twice as high as that of a traditional cutting system.
In this project, Donatoni concentrated not only on speed but also on the quality of cutting with the aim of developing a solution capable of producing ready-to-lay floors in a variety of custom sizes and with relatively short production times. Moreover, it grants higher safety and slab optimisation to reduce waste.
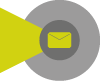
Did you find this article useful?
Join the CWW community to receive the most important news from the global ceramic industry every two weeks