New hi-tech frontiers for digital printing
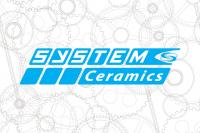
The Creadigit the single-pass drop-on-demand digital inkjet printer from System Ceramics - has established itself as a standard. Its electronics allow for high-speed printing and can create images of any kind with designs up to 200 square metres in size, making each surface truly unique.
In the field of digital printing, the global market now requires all-round solutions consisting of cutting-edge processes and increasingly interconnected hardware and software, to guarantee a high level of industrial automation and the utmost flexibility and customisation in accordance with the principles of lean manufacturing. For this reason, the digital printing process is like a well-coordinated orchestra, capable of creating aesthetically appealing ceramic surfaces with outstanding technical characteristics.
Thanks to intense research efforts, the Creadigit technology – the single-pass drop-on-demand digital inkjet printer from System Ceramics - has established itself as a standard. Its electronics allow for high-speed printing and can create images of any kind with designs up to 200 square metres in size, making each surface truly unique.
The printheads are the key components of the printing process. They are available in different versions according to native drop size, they have a resolution of 400 dpi, an internal recirculation loop and a high-resistance metal plate, and it can be fully reconditioned.
The printing process is a complex series of operations that use innovative hydraulic, electronic, mechanical and algorithmic control technologies that must work together simultaneously and in perfect synergy throughout the process. In this way, the operator can perform quantity-based printing with the important benefit of simple and immediate use. This means he can set the quantity of material to be deposited on the substrate, a very important factor because the quantity of ink can be changed without modifying the file that has been prepared for printing and with the guarantee that Creadigit will deposit the required quantity of ink.
Management of the jetting pulse is an example of the meticulous attention that is devoted to every aspect of the printing process, combining fluid dynamics studies with cutting-edge electronics. More than 1,000 inks have been tested and over 1,500 head-activation Waveform electronic tests performed to achieve optimal drop-on-demand digital inkjet printing.
The colour bar control electronics guarantee real-time management with the maximum synchronisation precision for high-definition printing.
The hydraulic and thermal circuits are designed to ensure optimal printhead feeding in the event of both high and low ink quantities. The system can determine the most suitable jetting conditions, thereby ensuring superior management of the quantity of ink to be deposited on the substrate. At the same time, the printheads are protected against risks (such as overheating and burning in the event of jetting without any material present) that System Ceramics has studied and overcome through hydraulic engineering solutions that leave nothing to chance.
The human-machine interface is simple and user-friendly thanks to the HMI platform developed in-house by System Ceramics and the COPILOT touchscreen industrial PC mounted on the front of the machine.
System Ceramics has also developed an innovative self-monitoring and vision system for the printing process called Creavision which monitors the tile when it enters the machine and adapts the graphic image to the tile’s real position to a precision of a tenth of a millimetre. Suitable for installation on any Creadigit machine, Creavision uses hi-tech video cameras to frame, analyse and control the position of the tile and ensure consistently perfect printing.
Towards “collaborative digitalization”
Today every printing machine must complete a digital process in which each ink contributes to the end result, for which purpose Creadigit can be fitted with 12 or more printing modules.
However, System Ceramics has now turned its attention to a new collaborative digital printing concept in which the process is even more flexible and adaptable and is based on a modular printing infrastructure distributed along the same line.
The future of digital printing will involve a system of independent machines each equipped with their own set of inks positioned in sequence along the production line. This arrangement will allow for greater creative freedom but at the same time will require an adequate technological infrastructure. System Ceramics has been carrying out specific research for this purpose and will soon proceed to the first installation of a Collaborative Full-Digital line.
The equipment necessary for this new approach has been developed in-house and will consist of systems fitted with software to further enhance creativity, resulting in a unique, high added value ceramic printing process.
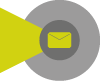
Did you find this article useful?
Join the CWW community to receive the most important news from the global ceramic industry every two weeks