RIEDHAMMER: Energy efficiency in sanitaryware kilns
Energy efficiency in sanitaryware kilns is one of the main selection criteria when considering new investments. To this regard, Riedhammer offers cutting-edge innovation and specific technical solutions, meant to reduce the environmental inpact and the increasing energy costs.
The main measures for enhanced energy efficiency in new plant include:
- energy-efficient engineering (EEE),
- energy-management-system (EMS) and Reko burner system,
- integrated process control,
- internal heat re-use,
- combined re-use of thermal energy,
- co-generation as a flexible and high efficient way to use available energy sources and recovery of waste energy.
Furthermore, there are also technical alterations possible to existing kiln plant which can be realized with varying investment costs and effort to achieve more energy efficiency, such as:
- high product setting density,
- directly re-used waste heat from the cooling zone,
- implementation of heat exchangers for the heat recovery,
- upgrade to pre-heated combustion air or secondary air.
The main objective of the developments presented under the terms EMS, Reko system and Co-generation consist in the significant energy savings combined with CO2 emission reduction and improved glaze quality on continuously and discontinuously operated kiln plants for sanitaryware production.
Apart from the possibility of using the waste heat from the kiln plant for other purposes to improve the energy balance of the factory, the EMS presents the latest technology for optimizing the use of resources such as gas and electrical power which also contributes to an increase in product quality. Due to various hardware and software tools contained within the system, which interact with the state-of-the-art kiln components, an extremely high performance level can be achieved to meet customers' demand for ecological and economical production plants for firing sanitaryware.
The table shows the energy and CO2 saving potential.
Type of kiln |
Specific energy consumption |
Riedhammer Tunnel Kiln |
510 to 680 |
Riedhammer Roller Kiln |
470 to 600 |
Riedhammer Shuttle Kiln |
890 to 1100 |
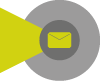
Did you find this article useful?
Join the CWW community to receive the most important news from the global ceramic industry every two weeks