Sanitaryware: New Tenagreen binders with low rheological impact
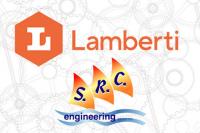
The new Tenagreen binders by Lamberti allows for improving the mechanical characteristics of the cast pieces while having a minimal impact on slip rheology, allowing for rapid and problem-free adoption on existing production lines.
In ceramic sanitaryware production, the potential for improving the mechanical characteristics of cast pieces simply by adding a chemical auxiliary to the slip is often limited by the significant rheological alterations caused by the additives currently available on the market. These alterations have to be corrected through adjustments to the production process, an operation that producers often consider too laborious or costly.
As part of its Tenagreen series, Lamberti has recently developed several new products that significantly improve the mechanical characteristics of the cast pieces while having a minimal impact on slip rheology, allowing for rapid and problem-free adoption on existing production lines.
Following an initial screening operation carried out in its own laboratories, Lamberti asked S.R.C. Engineering (a well-known technology consultancy firm that has been operating in the international ceramic sanitaryware sector for decades) to carry out its own laboratory assessment of three new-generation Tenagreen products with different chemical properties.
The tests
A standard vitreous china body slip prepared industrially by a leading Italian manufacturer was used for the tests. The slip was brought to a standard casting density of between 1800 and 1810 g/l. The products to be tested were subsequently added to the mixture and homogenised using a mechanical stirrer.
Along with the reference body, the following products and dosages were tested:
- Tenagreen CS 555, at dosages of 0.5% and 1% of dry content
- Tenagreen WW 01010, at dosages of 0.55% and 1.1% of dry content
- Tenagreen WW 01038, at dosages of 0.7% and 1.4% of dry content
The tests gave the following results:
- Viscosity: minimal variations in the viscosity value for all evaluated products.
- Thixotropy: a limited decrease in thixotropy is observed for CS 555 and an even smaller decrease for WW 01038, while WW 0100 showed a certain increase at low dosage and a limited reduction at the highest dosage.
- Thickness formation: at low dosages, the values are equivalent to or better than the standard for all products. At high dosages, the values for WW 01010 and WW 01038 are lower than the reference values but tend to reach them after 90 minutes.
- Total shrinkage: no significant variations.
- Pyroplastic deformation: no significant variations.
- Water absorption after firing: no significant variations.
- Dry M.O.R. values: the increases are highly significant and proportional to the dosage for all products tested, ranging from +22% to +107% compared to the reference.
All three new products in the Tenagreen series brought about a significant improvement in the mechanical properties of the body for minimal variations in the rheological parameters.
In some cases, improvements in thickness formation were also observed, along with a mild deflocculant effect which could be exploited to slightly reduce the quantity of deflocculant used in body slip preparation.
At the dosages used in the tests (from 0.5% to 1.4% of dry content), the improvements in the observed mechanical characteristics (up to +107%) are generally higher than the levels normally sufficient to improve production yields by reducing cracking and breakages prior to firing. This means it may be possible, for industrial production, to use lower dosages than in the tests, further reducing the already low impact on the slip rheology.
All the tested products can therefore easily be introduced into existing production lines and are capable of improving the mechanical properties of the body before firing.
The best product for each individual user must be chosen on the basis of the test results obtained with the different body formulations and/or economic considerations linked to the optimal dosage and current cost of the products.
In the current situation of extreme instability in raw material costs and consequently in the prices of additives, manufacturers may find it very useful to be able to choose between several products that can all be easily introduced into the process in order to achieve the best possible benefit-cost ratio.
These conclusions have already been confirmed in several plants following the introduction of one of the presented products into the normal production process.
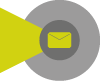
Did you find this article useful?
Join the CWW community to receive the most important news from the global ceramic industry every two weeks