Duravit invests in Sacmi technology in China and Egypt
Duravit’s Chongqing factory has been upgraded with the installation of pressure casting equipment for complex WCs as well as a fourth robot for automatic glazing. The fifth kils was started up in Egypt.
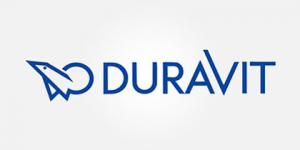
The remarkable growth achieved by Duravit in China has prompted the Hornberg-based multinational to make new technological investments in its Chongqing factory, one of the most modern and automated facilities in the country equipped with Sacmi plants for all production departments, from body preparation to the kilns, glazing lines and LGVs.
The latest projects have involved the installation of modern pressure casting equipment for complex WCs (RobotCasting), as well as a fourth robot for automatic glazing (the RobotGlaze system with the GA-OL robot from Gaiotto), which joins the three already supplied for the lines built in 2019. Along with improved product quality and process sustainability, Duravit also chose to adopt the anti-bacterial glaze application solution, an added value of RobotGlaze which is currently proving very popular in the market.
As for the casting department, Duravit has also opted for pressure casting for the production of highly complex WCs and bidets after using the solution for washbasins and cisterns. The chosen solution is AVI, the single-mould casting machine that stands out for its production flexibility and rapid mould change capability. The scope of supply included two AVI cells along with four moulds and two new models. Work at the Duravit China plant will continue during 2022, with four new AVI cells already being shipped.
One of the most important investments made by Duravit in its other factories is the start-up of a fifth kiln in its plant in Egypt, where production output recently exceeded 2.5 million pieces per year, almost all of which were sold for export to overseas markets. As in the case of the four kilns installed in 2005, 2017 and 2018, Duravit once again opted for Sacmi-Riedhammer technology with an 8-module SSK 440/198-8 model equipped with innovative internal linings (cordierite-mullite refractory plates) which reduce the need for maintenance and improve the quality of the firing process. The kiln is equipped with a rapid cooling system which reduces the total first-fire cycle time to just 14 hours.
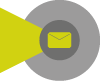
Did you find this article useful?
Join the CWW community to receive the most important news from the global ceramic industry every two weeks