DGINKS and HPLUS, Ferro solutions for more sustainable digital inks
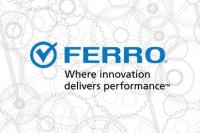
Ferro is presenting two new ranges of water- based inks that stand out for their improved emissions performance (including odorous emissions) during combustion: DG Inks - Decoration & Glazed Inks HPLUS).
The DG Inks family consists of “water-compatible” products which, unlike the Ferroinks 3.0 family, develop a certain quantity of water during combustion in the kiln due to the presence of hydroxyl groups in the chain. This means that the total quantity of carbon (CO and CO2) measured at the flue is slightly lower than in the case of Ferroinks 3.0 but even more importantly that odorous emissions during combustion are around 30 times lower. Because the DG Inks medium contains glycols, chains with carbonyl groups may be produced during the kiln pre-heating stage according to the reaction environment; in this case, the production of this type of molecule can be minimised by altering the firing conditions.
DG Inks almost completely lose their organic phase before reaching 250°C. This means that their oxidation time is much shorter than that of the Ferroinks 3.0, which therefore release a larger quantity of unburnt molecules into the flue.
As they do not contain “free” water and have an electrical conductivity of almost zero, DG Inks can be loaded directly into machine/ printheads already on the market without any particular need for adaptations. All that needs to be done is to clean the machine first with the old ink cleaner and then with the cleaner specifically formulated for DG Inks. The rheology and consequently fluid-dynamic behaviour of the ink has been specially designed to be used with the current digital printing machines once duly upgraded.
HPLUS inks on the other hand contain a significant percentage of water, which considerably reduces flue emissions compared to both Ferroinks 3.0 and DG Inks. The level of odorous emissions is one of the lowest in absolute terms, as is the total quantity of carbon measured.
As in the case of the DG Inks family, a limited degree of short carboxyl chain formation was observed at the flue (the quantity was in fact extremely small due to the firing conditions used for the samples, which are not comparable to those adopted at an industrial level, so an even smaller quantity of molecules other than water, CO and CO2 is expected).
The HPLUS inks are likewise designed to have the same rheological and colorimetric characteristics as the Ferroinks 3.0 series, although they can only be used on machines and printheads that are specially designed to function with a high water content (corresponding to a high level of electrical conductivity and a higher degree of evaporation than the 3.0 series).
The HPLUS family also includes HPLUS1, HPLUS5 and HPLUS10. These specific classes of inks stand out for their larger particle size compared to traditional inks. The HPLUS1 inks (with particle size of a micron or smaller) include colour inks and material inks and guarantee the same levels of performance as applications already in use but in a water- based solution.
Inks with larger diameter particles such as the HPLUS5 are able to produce more intense colours. Moreover, in terms of material application they come close to the results achieved with traditional methods but without any risk of toxicity due to the submicronic milling. The HPLUS10 inks further extend the range of possibilities in terms of both colour and material, but they are still undergoing study, particularly regarding the correct choice of printhead.
This new inkjet technology will be shortly introduced in the ceramic market; the coming months will be used to develop the necessary experience to size its impact on the current digital decoration technology.
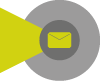
Did you find this article useful?
Join the CWW community to receive the most important news from the global ceramic industry every two weeks