Efficiency and the sustainable transition: how the finishing process is evolving
BMR is proposing a new approach to control the finishing stage, based on full integration into a digital service platform. The aim is to optimise every stage, reducing waste and guaranteeing greater efficiency and consequently improved margins.
BMR’s commitment to pioneering research and development in end-of-line processes has become synonymous with a mission dedicated to delivering the highest levels of performance. This mission integrates quality, innovation, automation and sustainability in accordance with the most rigorous green technology standards. BMR’s technologies are becoming increasingly efficient and competitive thanks to a high level of synergy between processing plants, machines and accessories. The result is a complete and fully customised ceramic end-of-line process, meticulously tailored to the unique requirements of each company.
Through its tireless R&D efforts and collaboration with leading international ceramic tile producers, BMR has developed a series of top-performance and extremely competitive technologies and patents for each step in the finishing process.
To achieve total control over the entire production process, especially the finishing stage, BMR is proposing a new approach based on full integration into a digital service platform. By creating systems that allow for objective data analysis and optimal machine settings, BMR aims to optimise every stage in the production process to ensure maximum objectivity, thereby reducing waste (in particular by avoiding the loss of batches of slabs due to chipping, processing errors or lapping) and guaranteeing greater efficiency and consequently improved margins.
This philosophy has driven BMR to develop its two flagship products: SuperShine Plus and Squadra Vision.
SuperShine Plus
Like other finishing operations, the dry polishing process has also completed the transition from analogue to digital with the development of SuperShine Plus, the latest iteration of the first SuperShine model developed by BMR more than 10 years ago. Building on its success in various markets, SuperShine Plus is able to guarantee ever-higher standards of quality and efficiency and has its sights set firmly on the future.
SuperShine was to all intents and purposes the first super dry polisher available on the market. With an operating process based on the mechanical and physical interaction between the tool, the surface and the applied chemical product, the machine is designed to enhance the digital graphics of the tile and give the surface a high gloss level and high degree of protection.
The latest version stands out for its high performance, its environmental friendliness and above all the fact that it is ultra-connected, with constant data sharing for the purposes of process control. This model will integrate two functions: the aesthetic function of polishing based on the mechanical action of the tools, and the protective treatment resulting from the closure of the surface pores. SuperShine Plus is the first and only dry super-polisher that can guarantee these two functions along with digitalisation of the entire polishing and treatment process.
The new digital component allows the machine to use the satellite heads via software to apply a product A, such as a surface protector which bonds mechanically to the treated surface and closes the porosity by means of a filling and sealing process. Depending on market requirements, the customer may also decide to use a product B to give the surface specific functions.
SuperShine Plus will therefore provide a number of advantages, including levels of performance and versatility that could not be achieved with traditional systems, largely thanks to modules with 10, 12, 16 and 10+10 heads.
Placing the new super polisher at the centre of the new finishing department will improve the efficiency and productivity of the line, reduce fixed production costs and significantly improve the quality of the ceramic surface due to its ability to remove finishing defects such as streaks, feed marks and fine scratches. As mentioned above, the use of new tools optimises resources and reduces waste.
Squadra Vision
BMR is introducing a new concept in the ceramic end-of-line stage, resulting in the development of a new product line. The first machine in this latest range developed by the company is the new Squadra Vision.
Energy efficiency, environmental sustainability and supply chain development are just a few of the innovative aspects of BMR’s Squadra Vision range, which results in an increasingly objective and sustainable process that uses digital cameras to monitor operation and thereby conserve energy resources and cut costs.
The latest iteration of BMR’s classic squaring machine featuring the use of video cameras, Squadra Vision is an advanced, highly automated and meticulously engineered system. As a result of continuous technology upgrades, it embraces the concepts of the Smart Factory and Industry 4.0, bringing numerous advantages in terms of energy savings, eco-sustainability and reduced production costs. Tests conducted at customers’ sites have shown that for the same material, removal rate and speed, this camera-based technology has 40% lower grinding wheel consumption than laser-based or similar technologies.
Squadra Vision is a dry squaring machine with 9 or 12 calibrating units per side, ideal for all types of materials and sizes up to 1800x3600 mm or larger. The new state-of-the-art version with measuring camera system is capable of monitoring the squaring operation in real time and detecting chipping defects. In addition, the use of displays combined with automatic advancement of the calibrating spindle, which is equipped with a brushless drive system and belts, makes it possible to determine the precise position of the tool and ensure that it operates automatically once the operator has set the material removal cone. This way, the system corrects the tool’s working position and optimises its effectiveness while maintaining size and productivity settings. In practical terms, the degree of material removal can be changed quickly and easily according to the configuration and type of tool mounted on the squaring machine.
BMR’s patented camera-based system is the only solution of its kind that has been applied to a squaring machine, and it has already been upgraded.
Squadra Vision is designed to combine high performance with significant benefits in terms of the environment, energy savings, consumption and tool cost. Equipped with a laser system at the line infeed and outfeed, the machine automatically controls numerous functions and parameters, ensuring a higher percentage of first choice products and consequently a reduction in labour and process costs, while at the same time respecting the environment and complying with sustainability standards.
Squadra Vision provides the following innovative features:
- new release of the machine software;
- new higher performance spindle capable of operating at lower temperatures;
- next-generation cameras with improved image speed;
- freeze frame function with chipping recognition and incorrect grinding wheel operation detection;
- fully automatic operation that enables the machine to function completely independently;
- improved automatic cleaning of the camera system with complete dirt sealing and waterproofing;
- grinding wheel savings (from 25% to 40% less consumption);
- bevel position feedback controlled by measuring profilometers;
- improved and intuitive machine maintenance;
- optimised quality: less chipping or breakage, less downtime, greater continuity of production and less wastage of material during size changes;
- constant process control: less operator intervention and greater focus on problem-solving;
- consumption and production data monitoring: all information on the consumption, lifetime and efficiency of the grinding wheels is continuously recorded and saved;
- the systematic use of increasingly eco-friendly technologies encourages everyone involved in the production chain, including employees and suppliers, to adopt green and sustainable technological solutions.
Through a holistic vision of the production process, BMR technology ensures perfect synergy between the lines and therefore maximum productivity. The ability to control almost all production procedures internally allows for the development of increasingly customised solutions, with a strong focus on digitalisation and eco-friendly automation. The customer takes centre stage in this process as part of a global-oriented vision, backed throughout by the guarantee of Italian quality.
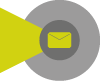
Did you find this article useful?
Join the CWW community to receive the most important news from the global ceramic industry every two weeks