Form and function: the new age of digital ceramics
Today’s interior design trends are increasingly shaping ceramic products, a transformation which has been made possible by a series of innovative solutions developed by Sacmi, including surface and body decoration, surface structuring and synchronisation of the various digital applications.
The continuous evolution of living styles is a powerful driver for the development of new ceramic products that better meet the needs of modern homes. Today’s interior design trends – from new luxury to technology and nature – are increasingly shaping ceramic products, compelling them to take on new forms and functions. This transformation has been made possible by a series of innovative solutions developed by Sacmi, including surface and body decoration, surface structuring and synchronisation of the various digital applications.
So what are the key developments in interior design that most clearly demonstrate the close relationship between furniture and ceramic surfaces?
First, the emergence of the total look concept has prompted ceramic products to evolve beyond traditional floor and wall applications to become fully integrated design elements, including worktops, furnishing components and finishings. The total look concept extends beyond interiors, creating a sense of continuity between indoor and outdoor spaces. Over the years, outdoor areas have gained significance and are now designed with the same level of attention as interiors, reinforcing the role of ceramic surfaces as a key design element.
Extending the use of ceramic floor and wall coverings to external applications has required specific research into new surface solutions, particularly those capable of realistically reproducing natural stone with three-dimensional textures and finishes. In this context, Sacmi’s advanced surface structuring technologies, combined with surface decoration and post-firing treatments, allow for the creation of exceptionally natural-looking stone surfaces with outstanding technical and aesthetic properties. New techniques for synchronising the multiple digital applications play a key role in this process as they ensure perfect integration between the surface and the body of ceramic products.

Surface structuring
Sacmi offers two possible solutions for creating surface structures. The first is the traditional structured belt used on the Continua+ line, while the second is the Deep Digital Line, which integrates the DDG glue and grit decorating machine with the DHD digital printing machine. Specifically, at the exit from the Continua+ line, the first DDG performs digital structuring using resist inks and grits. This is followed by the DHD, which prints inks, resist inks and effects. Finally, the second DDG performs digital decoration with grits. To ensure precise synchronisation, the process incorporates an advanced electronic centring vision system called Line Up, which aligns and centres images with extreme precision, synchronising the various printers along the production line and allowing for the creation of exceptionally high-quality multi-layer products. At a higher level of line management, the Line Manager system provides a unified interface for the integrated control of all graphic files and digital decorating machines in operation within a single factory or across multiple facilities owned by the same company.
Combining the Deep Digital Line with the Line Up and Line Manager systems allows unlimited potential for customisation, resulting in unique, tailor-made ceramic surfaces with perfect finishes and sharp details achieved through automatic image alignment. At the same time, the systems ensure maximum production efficiency with optimised processes and shorter production times.
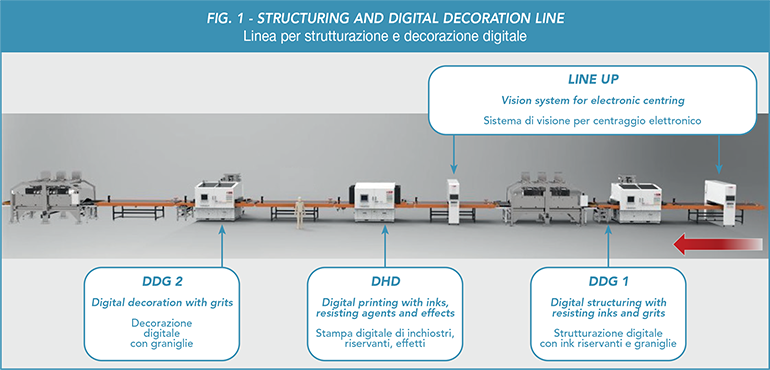
Post-firing processing
Post-firing treatments play an equally important role in enhancing ceramic surfaces. The technologies developed by Sacmi Group member company BMR allow for exceptionally high-quality polishing, satin finishing and crest lapping. These processes are now complemented by innovative solutions such as WoF (from Surfaces Group), which imparts a uniquely soft and silky touch to ceramic surfaces, making them ideal for a wide range of applications.
V-Nature, the through-body veining line
New ceramic applications – ranging from kitchen countertops and furniture (such as tables, consoles and bathroom fittings) to ornamental items – require three-dimensional decoration. This means decorating the ceramic body using powders, flakes and material mixtures, all synchronised with digital surface printing.
To create these products, Sacmi has developed V-Nature, a through-body veining technology that performs three-dimensional decoration prior to compaction using a V-Nature feeder. This is followed by continuous on-belt pressing with the PCR compactor and through-body vein vision systems that synchronise the subsequent DHD and DDG digital printers.
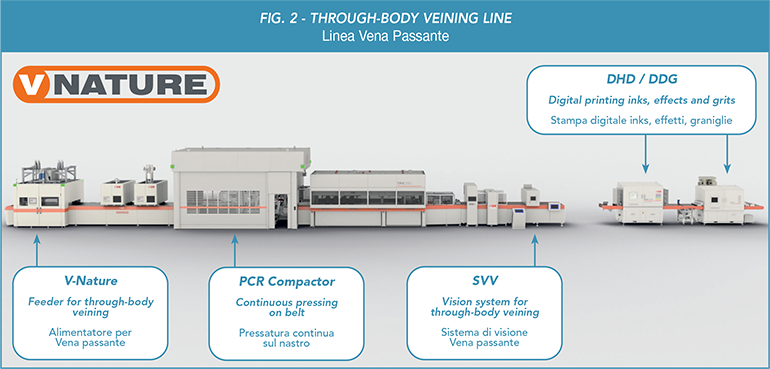
This advanced technology allows for the production of exceptionally high-quality ceramic products that closely resemble natural stone and other materials. Several examples are showcased at Sacmi’s Tiles Lab in Imola, including travertine-effect ceramic slabs, furnishing items and designer washbasins created from 20 mm thick ceramic slabs. The decorative effect is clearly visible on all sides of these slabs, making them effectively double-sided.
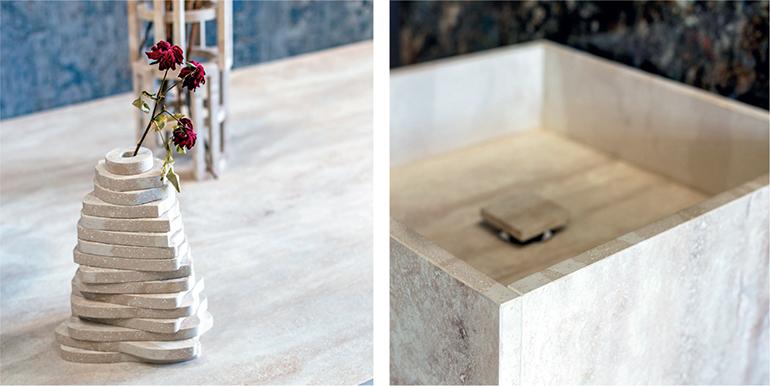
At Tiles Lab, the pursuit of new solutions and innovative products is an ongoing process. In collaboration with leading frit and glaze producers, Sacmi has successfully created a complete range of through-body veined products, including wood, stone, travertine and designer collections, several of which were exhibited at Tecna 2024.
In the field of two-dimensional decoration, solutions have been developed for indoor and outdoor marble and stone applications. These integrate traditional digital decorations with glue and grit applications, followed by surface finishing treatments using technologies from BMR and Surfaces Group.
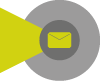
Did you find this article useful?
Join the CWW community to receive the most important news from the global ceramic industry every two weeks