DPD (Digital Product Development) by SACMI: the rise of digital modelling in the sanitaryware industry
The number of moulds made using the innovative “by tooling” process continues to grow, and, for the first time, supersedes the traditional “by casting” system.
Last November, Sacmi Sanitaryware reached a significant milestone with the production of mould number 7,400, delivered to a leading Italian producer that has adopted Sacmi technology throughout its production process for the past twenty years.
This mould, like 80% of those manufactured by Sacmi in the year 2024, was produced using the tooling method which involves direct milling of porous resin blocks via CNC work islands.
Known worldwide for the design and development of porous resin moulds, Sacmi Sanitaryware has made significant advances in this technology in recent years. Alongside the traditional casting process, where moulds are produced from a case mould, Sacmi has increasingly adopted the tooling system. This approach drastically reduces mould development times while enabling the mould production department to operate continuously without personnel, as workstations can run 24 hours a day unmanned.
Over the past five years, Sacmi has produced approximately 250 moulds using the tooling method. This technique continues to gain popularity and last year surpassed the casting technique, with 8 out of 10 moulds created using this innovative method. In 2024, Sacmi took a further step forward with the introduction of the innovative digital casting method, which involves direct milling of polyurethane blocks to produce the case mould.
Sacmi’s ability to produce increasingly complex moulds using this innovative system has enabled it to expand its target market as part of its new Digital Product Development strategy. This digital modelling approach supports customers at every stage of the process, integrating traditional casting methodology with the innovative tooling and digital casting systems to achieve complete digitalisation throughout the production cycle.
This latest achievement strengthens Sacmi’s role as a comprehensive partner capable of offering expertise in casting technologies and mould design and production. Through its original solutions, Sacmi helps customers develop modern, innovative products while maintaining a high level of quality, optimised lead times and cost efficiency.
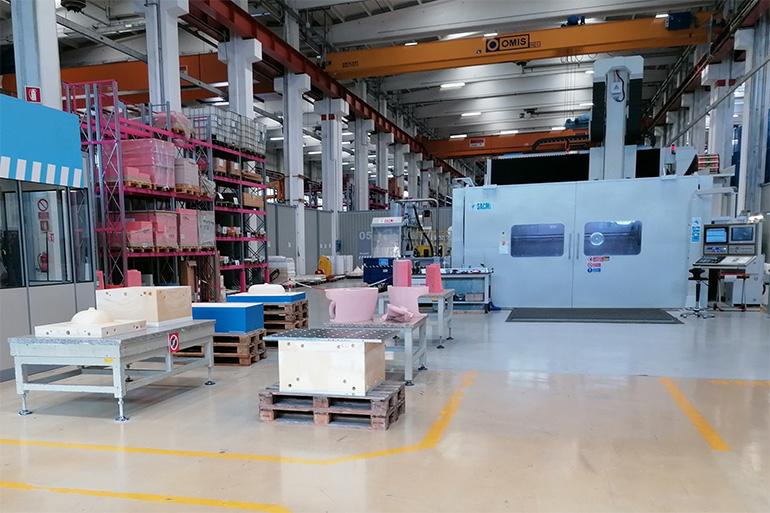
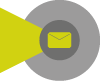
Did you find this article useful?
Join the CWW community to receive the most important news from the global ceramic industry every two weeks