Garoll: sanitaryware service
The Garoll HPC-201HT pressure casting system was developed to meet the needs of producing solid and drain cast sanitaryware from two-part moulds. The versatility of the new press, the latest development of the highly successful HPC-201 series, is able to perform solid or drain casting and demoulding either horizontally or vertically. This enables it to produce all types of solid or drain cast sanitaryware with two-part moulds in different sizes (up to 2000x1800 mm free space for the mould). The new press is equipped with an assembly of two mould supports which can be customised according to production requirements, a system for rotation of the mould supports and various accessories according to the type of moulds installed. With a fully automatic PLC-controlled casting cycle, mechanical movement of the mould support, robotised demoulding and production flexibility guaranteed by effective customisation of the machine, it is possible to create fully automatic production units with high output. The new unit HPC-201HT guarantees the highest levels of production process flexibility and can be supplied in various versions according to production requirements.
The most significant technical characteristics are: variable sizes of the mould support according to the size and number of pieces that are to be produced; possibility of rapid mould changing using the Garoll MRC® system; simultaneous opening of the two semi-moulds; machine settings stored in the PLC for rapid setup of all production parameters for the installed mould.
The construction of the basic module of the HPC-201HT consists of a loadbearing structure that interfaces directly with the mould support beam and mould support and movement units, one of which consists of a beam on which are mounted servo-guided slides equipped with arms that hold the mould supports. A body feeding circuit and the auxiliary circuits allow the services required for press casting operations to be performed.
![]() |
![]() |
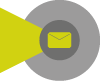
Did you find this article useful?
Join the CWW community to receive the most important news from the global ceramic industry every two weeks