LB HYBRID: The sustainable future of ceramic body preparation
Successfully launched at Tecna 2022, LB HYBRID technology allows to save up to 65% thermal energy and up to 70% water and reduces atmospheric emissions by up to 65%.
LB HYBRID is a brand new ceramic body preparation solution designed to optimise production costs through energy savings while ensuring the highest levels of environmental sustainability. Successfully launched for the first time at Tecna 2022 in Rimini, this technology has been judged by many operators one of the most interesting technological innovations on show at the fair.
This patented technology combines dry and wet milling and guarantees maximum plant flexibility by adapting to any manufacturer’s needs. In this new process, the powder obtained from dry milling is homogenised together with the wet milled slip to create a microgranulate suitable for pressing. The microgranulation process occurs by means of nucleation and accretion of dry ground powder when slip is injected into the granulator using dedicated nozzles.
Specific powder/slip proportions are maintained and care is taken to ensure that the parts have the same composition. Granulation takes place inside the new HGT (Hybrid Granulation Technology) continuous microgranulator. The microgranulate is subsequently returned to a moisture content suitable for pressing.
Characteristics and advantages
LB Hybrid technology allows production area usage to be optimised as it occupies less space than traditional systems. Industrial tests have shown that microgranulate obtained with LB Hybrid technology has the following characteristics:
- particles with equivalent levels of flowability to the powder from standard technology;
- possibility of producing tiles of any size and thickness using any shaping technology currently available on the market;
- finished porcelain stoneware products that comply with standards;
- controlled particle size curve;
- ceramic tiles with excellent surface quality.
The tile surface obtained with microgranulate produced using LB HYBRID technology showed excellent characteristics and is compatible with all decoration systems.
The LB HYBRID microgranulate has similar technological characteristics to powder from standard technology (Table 1).
Compared to a traditional body preparation process, LB HYBRID technology saves up to 65% thermal energy and up to 70% water and reduces atmospheric emissions by up to 65%.
Taking as an example an annual production of 5,000,000 m2 of 10 mm thick tiles, LB HYBRID reduces CO2 emissions by 6,000,000 kg/year and allows for water savings of 30,000,000 litres/year, assuming an average tile moisture content of 10.5% and a slip moisture content of 32%.
ATM |
TEST 1 |
TEST 2 |
TEST 3 |
TEST 4 |
Powder range |
Greater flowability when: |
|
Moisture content of powders (%) |
6.6 |
6.6 |
9.5 |
6.7 |
6.8 |
4-8 |
Irrelevant |
PD (g/cm3) |
0.928 |
1.015 |
1.043 |
1.006 |
1.039 |
0.92-1.05 |
See HR |
TD (g/ cm3) |
1.062 |
1.191 |
1.211 |
1.179 |
1.225 |
1.03-1.13 |
See HR |
HR (1) |
1.14 |
1.17 |
1.16 |
1.17 |
1.18 |
1.07-1.17 |
HR low (<1.25) |
ARS (°) |
25.5 |
27.2 |
26.8 |
28.3 |
26.5 |
30-35 |
ARS low (<45°) |
ARD (°) |
46.6 |
49.0 |
56.5 |
46.9 |
50.0 |
40-45 |
ARD low |
Bulk Flow |
13.0 |
15.6 |
16.4 |
15.3 |
15.8 |
13-16 |
FdM high |
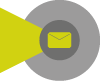
Did you find this article useful?
Join the CWW community to receive the most important news from the global ceramic industry every two weeks