Bedeschi: robotic grippers with low weight and high gripping strength
The new grippers can be adapted to a wider range of anthropomorphic robots for handling wet, dry and fired clay products.
The new robotic grippers developed by Bedeschi’s R&D team are lighter, stronger, capable of preventing wear of spare parts and guaranteeing maximum grip elasticity so as to prevent deformation and/or breakage of handled products.
They can be adapted to a wider range of anthropomorphic robots for handling wet, dry and fired products. The grippers stand out above all for their low weight, a characteristic that enables them to handle a greater quantity of material with significantly lower energy consumption.
This highly innovative project is the result of the Padua-based company’s expertise across a variety of industrial sectors and its more than a century of experience in the field of handling and automation for the heavy clay sector.
A solution for every customer
The new robotic grippers were recently included in three orders from leading brick manufacturers to modernise their stacking, unstacking and packaging systems. The projects stood out for their rapid service and high degree of customisation and were all completed successfully and to the total satisfaction of the customer.
For the Wienerberger Group, the company designed a series of special pneumatic grippers for robots to replace the existing obsolete and underperforming models.
To meet the customer’s needs, the new grippers are manufactured with a special aluminium alloy to ensure higher performance and lower weight. Each gripping wall is equipped with a series of independent hardened stainless steel blades complete with special rubber pads to ensure a superior grip and greater adaptability to size differences. In addition, a special compensation system was supplied to ensure correct layer positioning during stack formation on the kiln car.
Another major UK-based facing brick manufacturer commissioned Bedeschi to study and supply a flexible solution for reducing the number of machines installed on the handling lines so as to reduce consumption and some of the maintenance work. The installed line includes two new automatic setting robots for dried product, each equipped with independent ten finger grippers, each of which is servo controlled to allow for customised setting of pattern configurations on each individual layer. The grippers can be supplied complete with an automatic rapid change system operated directly by the robot without operator intervention. Each robot will have an area for automatically parking the grippers used for handling the various products and/or sizes.
Finally, as part of a project to modernise one of the production sites of a well-known Italian construction materials manufacturer, Bedeschi replaced the existing dry product setting grippers with two new traditional five-head grippers featuring pneumatic and rotating heads. This order followed the previous installation of a gripping device at another of the group’s facilities.
Sustainable development and the Industry 4.0 transition are the two main goals
As in the past, Bedeschi is focusing on sustainability with the aim of increasing the energy efficiency of its technological solutions. In recent years, the company has developed a complete line for filling bricks with granulated mineral wool, an environmentally friendly solution that delivers excellent thermal insulation performance, and has built a line for the production of prefabricated walls ready to be assembled on site with exceptional time savings.
The company has also recently developed fully automatic lines for handling different types of products from single bricks to stacks of bricks, roof tiles and accessories, all in accordance with Industry 4.0 principles.
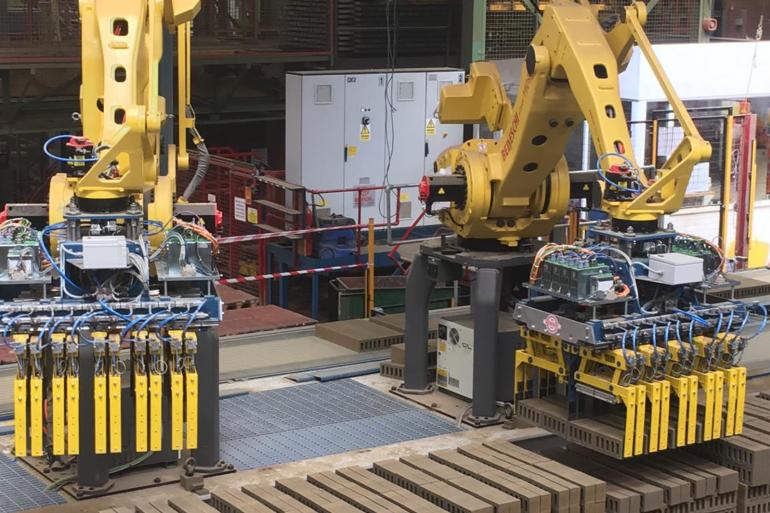
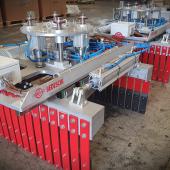
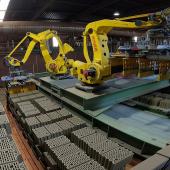

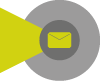
Did you find this article useful?
Join the CWW community to receive the most important news from the global ceramic industry every two weeks