System automation for the end-of-line
Automation plays a key role in achieving production process efficiency.
For the end-of-line stage of tile manufacturing, System has developed a series of patented process systems controlled by management software. This creates an invaluable archive of information and statistics which are vital for comparing new and previous production processes.
The approach followed by the group is to focus on electronics, designed and built entirely by System Electronics, together with production data analysis and a search for process systems that allow for savings in parts (wear components), raw materials and energy.
System automations for the ceramic end-of-line stage begin with the integrated Qualitron system, which determines tile quality by detecting defects, size and flatness. The lighting systems are combined with vision systems and video cameras which rapidly detect any colour issue thanks to the colour acquisition configuration. Using the simple interface, the operation can change the parameters instantly and use the self-learning programs to teach the machine the levels of acceptability.
After passing the Qualitron control point, the tiles are stacked by the sorter according to their class. The latest addition to System’s range of machinery is the fast and quiet Multigecko sorting line (noise levels have been cut by two-thirds), equipped with a variable number of pick-up points - from 1 to 8 depending on the product to be handled in the factory. This sorting line is proving increasingly popular, firstly because it sorts and chooses products and stacks them on two sides, and secondly because it is capable of handling large sizes up to 1200x1800 mm in keeping with the current demands of the market.
The tiles are then packaged directly within the machine by 4Phases, a packaging machine that wraps cardboard around the stack of tiles (resulting in up to 80% cardboard savings), prints four-colour logos and texts, eliminates the costs of cardboard blank storage, and reduces the CPI coefficient.
The boxes are sent to the Falcon palletiser which arranges them on the pallets according to their class. When completed, the automatic fork-lift vehicles (AGVs) engage the pallet and move it to the warehouse or towards the pallet finishing line.
System automation therefore ensures complete and high-performance management of all production steps between quality control, end-of-line and transfer of the finished product to the warehouse.
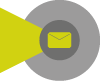
Did you find this article useful?
Join the CWW community to receive the most important news from the global ceramic industry every two weeks