Sistema di raffreddamento piastrelle "Igloo Cube 3.0" di Tekmak
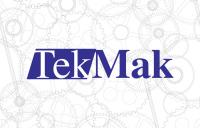
A partire dal 2012 Tekmak è stata la prima azienda nel mondo a sviluppare un sistema brevettato, nato e pensato per il raffreddamento delle piastrelle ceramiche in entrata alle stampanti digitali: Igloo. Nel 2014 è arrivata la versione 2.0: il sistema Igloo Combo. Ad oggi si contano circa 200 Igloo, nelle due versioni, installati in 26 paesi.
La ricerca Tekmak in questo settore non si è fermata e oggi l’azienda presenta Igloo Cube, la versione 3.0, ossia la versione più innovativa e rivoluzionaria in termini di consumi energetici, dimensioni e prestazioni. Igloo Cube permette di raffreddare le piastrelle prima della stampa digitale togliendo un’altissima quantità di umidità presente nella parte di smalto applicata sul supporto ceramico, e abbassando in modo determinante la temperatura dello smalto applicato sulla piastrella in modo da creare le condizioni ideali per ogni tipo di stampante digitale. Igloo Cube si basa sulla tecnologia di raffreddamento a scambio diretto. Si presenta quindi come una macchina estremamente compatta, di dimensioni ridottissime (1460x1700mm e solo 1400mm in altezza), per essere posizionata lungo ogni linea di smalteria, anche le più corte e le più accessoriate.
La macchina viene montata sulla linea di smalteria senza necessità di interromperla e lasciando libera e pulita la parte sotto il trasporto, fissata su un proprio telaio di sostegno.
Il sistema a scambio diretto è reso estremamente efficiente dalla tecnologia “full inverter” che permette risparmi notevoli rispetto a macchine simili, con consumi fino a tre volte inferiori agli attuali. Infatti, a fronte di una potenza installata di soli 11 Kw, a macchina funzionante si ha un consumo minimo di soli 2 Kw/h e un consumo medio orario a regime di soli 6 Kw/h, il più basso di qualsiasi tipo di raffreddatore.
L’esperienza di Tekmak nella costruzione di raffreddatori negli ultimi 4 anni ha permesso di ottimizzare una capacità installata estremamente contenuta con un’elevatissima efficienza di raffreddamento e blocco della produzione del vapore tramite il sistema brevettato Vortex AirFlow. In pratica, vengono sfruttate particolarissime geometrie di flussi d’aria che permettono di ottenere dei vortici d’aria a temperature inferiori a 0°C che impattano a distanza ravvicinata sulla piastrella a velocità di oltre 120 km/h. Il risultato raggiunto è di congelare superficialmente la piastrella, condizione che non consente il passaggio di vapore dal supporto alle testine della digitale, e di rendere lo smalto freddo e secco, in modo che la scrittura con la macchina digitale risulti senza alcun problema.
L’effetto è temporaneo, della durata di alcuni secondi, tempo sufficiente al passaggio sotto le testine della digitale. Igloo Cube installa un sistema di pulizia ultrarapido che permette la pulizia completa della macchina senza l’intervento dell’operatore in un paio di minuti. Non è quindi mai necessario fermare la linea di smalteria, dato che la pulizia di Igloo Cube è sempre sincronizzata con quella della stampante inkjet, collegando elettricamente la prima con un contatto alla macchina digitale.
La nuova macchina Tekmak è progettata non solo per le piastrelle di formato tradizionale, ma anche per le grandi lastre e gli spessorati. Può essere installato infatti un particolare sistema elettrico con telecamera che permette di mantenere la distanza ideale tra la piastrella e l’uscita del vortice di aria in base allo spessore della piastrella. Nel caso sulla stessa linea vengano realizzati formati e spessori diversi, il vortice d’aria avrà sempre la stessa distanza di impatto ideale. Igloo Combo è il primo raffreddatore realizzato con il sistema master/slave, che lo rende particolarmente valido proprio nella produzione di grandi lastre: è possibile realizzare un tunnel, di lunghezza 3.200 mm (o anche di 4.800 mm), sfruttando i comandi del pannello di controllo del PLC Siemens montato nella macchina Master, e implementando semplicemente la macchina dei moduli necessari.
Il nuovo raffreddatore migliora la qualità della stampa aumentando la vita delle testine, conservandole più pulite ed efficienti, e permettendo una produzione più fluida senza fermi macchina. Tutto ciò con i costi di esercizio più bassi tra le tecnologie esistenti.
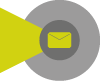
Hai trovato utile questo articolo?
Unisciti alla community di CWW per ricevere ogni 15 giorni le principali novità da tutto il mondo sul settore ceramico