Anteprima Tecnargilla - System: il Rotodigit di nuova generazione
In occasione di Tecnargilla, System presenta importanti novità per la decorazione digitale con un Rotodigit di nuova generazione, per il confezionamento con 4Phases, rivoluzionaria macchina per l’imballaggio delle piastrelle ceramiche, e, infine, la vasta gamma dei prodotti a basso spessore, realizzati con tecnologia Lamina, nonché la nuova macchina di taglio al laser Freesize.
Rotodigit è un sistema di stampa digitale che si applica sulle linee di decorazione Rotocolor. Con Rotodigit è possibile decorare qualsiasi superficie ceramica – anche strutture e bordi - con ottimi risultati nella riproduzione di pietre naturali, marmo e granito, nella decorazione su rilievi e superfici strutturate e in doppia pressatura. Caratteristiche salienti sono: la possibilità di effettuare la stampa sincronizzata con i rulli Rotocolor e di avere unità di stampa indipendenti per ogni inchiostro; un sistema di ricircolo inchiostro e di protezione teste di stampa; la disponibilità di tre diverse tecnologie di decorazione; la possibilità di raggruppare negli stessi ingombri diverse tecnologie, salvaguardando gli spazi disponibili
4Phases costruisce le scatole direttamente in macchina, partendo da un foglio di cartone neutro in piano e formando una scatola che si adatta al prodotto, assorbendo tutte le variazioni di calibro e di altezza pila. Preceduto da un sistema composto da controllo di qualità (Qualitron) e smistatore di nuova generazione, che preleva in automatico i pezzi identificati in classi omogenee trasferendoli su un pianale statico, forma direttamente in macchina il processo di confezionamento. Creando una striscia continua di cartone in macchina, 4Phases è in grado sia di costruire scatole per formati diversi con estrema velocità nell’operazione di cambio sia di personalizzare in macchina la stampa del cartone che viene eseguita prima della fase di chiusura della scatola. L’impianto Freesize cambia completamente il processo di taglio delle lastre, aumentando la produttività e riducendo gli scarti rispetto ad una lavorazione tradizionale; in assenza di acqua, la gestione del prodotto Laminam® è più pulita e non necessita di asciugatura, con notevole beneficio rispetto all’impatto ambientale.
Il taglio a secco avviene in tre fasi:
- La molatura, con cui si asporta la fibra di vetro nei punti di taglio, ad una velocità max di 60 m/min su un tavolo automatico a ponte a controllo numerico, con pianale fisso e cinghie per la traslazione automatica. I banchi di molatura, progettati da Lamina, salvaguardano l'ergonomia e la sicurezza dei lavoratori tramite una chiusura integrale con protezioni X. Anche il rumore e la polvere sono ridotti al minimo. La precisione nel movimento di posizionamento e asportazione sono garantite da sistemi di ultima generazione. A seguire, un ribaltatore automatico ruota le lastre di 180º, così da posizionare sul banco d’incisione il lato non stuoiato che verrà inciso nella parte superiore;
- L’incisione della superficie avviene su un tavolo a ponte a controllo numerico computerizzato, con massima stabilità e minime oscillazioni. L’incisione avviene tramite un nuovo sistema laser, studiato appositamente, con un’ottima resa e durata, e consente di mantenere una velocità costante di 60 m/min, anche sulle superfici più delicate per raggiungere picchi massimi anche di 110 m/min. Con il sistema laser si elimina ogni contatto con la superficie, azzerandone ogni danneggiamento e rischi di eventuali micro sbeccature, particolarmente problematiche nei prodotti con grafiche complesse o superfici strutturate fino ad oggi inavvicinabili;
- La troncatura della lastra in corrispondenza delle linee di molatura-incisione, per creare i formati desiderati. Gli sfridi di testa, di coda e laterali passano allo smaltimento tramite nastri frantumatori. La lastra viene allineata e trasportata, con sistema a rotelle, verso il troncatore dinamico, che apre l’incisione, tramite la pressione dei rulli separatori. All’uscita, i pezzi vengono distaccati con una rulliera motorizzata a velocità variabile. Posizionate e centrate, le lastre passano sul nastro della macchina di carico pezzi.
- Il controllo di tutte le operazioni è affidato ad un efficientissimo sistema elettronico di ultima generazione firmato Bekcoff.
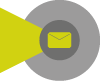
Hai trovato utile questo articolo?
Unisciti alla community di CWW per ricevere ogni 15 giorni le principali novità da tutto il mondo sul settore ceramico