Sacmi Whiteware supports Italian sanitaryware manufacturers in the transition towards Industry 4.0
Hatria, Ceramica Flaminia and GSI continue their journey towards total sanitaryware factory automation with Sacmi.
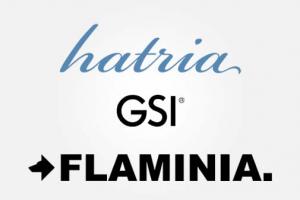
The latest investments made by leading Italian sanitaryware manufacturers have focused on Industry 4.0 and total automation. In particular, Hatria, Ceramica Flaminia and GSI (Gruppo Sanitari Italia) have chosen Sacmi technology to improve the efficiency of their plants while focusing on digitalisation, quality, productivity and safety.
Hatria (Teramo), a Sacmi customer for more than twenty years, has doubled the output of its shower tray casting line by starting up a second ADS machine with RobotCasting technology devoted to the production of thin shower trays of various sizes (up to 140x90 cm, the most popular size in the market) with either a traditional glossy glazed finish or a natural stone effect. Along with the increase in productivity (almost 350 more pieces/day when fully operational), it has also raised the level of automation in all casting and handling operations thanks to the integration of robots and LGVs. A further step towards creating a complete Industry 4.0 factory is the adoption of the RobotClean system for robotic sanitaryware finishing, a solution designed to replicate the most complex piece finishing tasks traditionally carried out by hand and make them fully repeatable. The cleaning station is totally isolated from its surroundings and is also equipped with water curtain filters to facilitate the removal of any residual dust, thereby ensuring that the robot work area is kept perfectly clean at all times.
Another highly ambitious project is the technological upgrade carried out by Ceramica Flaminia (Civita Castellana), a company that has been working with Sacmi for several years as part of the Industry 4.0 transition of all its production phases. The company has once again opted for a Sacmi robotic casting solution in the form of a new AVB machine for rimless WC production, equipped with a demoulding robot and capable of mounting up to 4 moulds. One of the key features of the new solution is the innovative method for handling pieces with undercuts consisting of an insert that allows these special geometries to be produced directly in the machine without the need to glue on additional parts. Thanks to the new AVB (and a second machine which is already planned), Flaminia will be able to manage a large number of product codes on complex pieces in an efficient and repeatable way and achieve a productivity at full capacity of approximately 200 pieces/day.
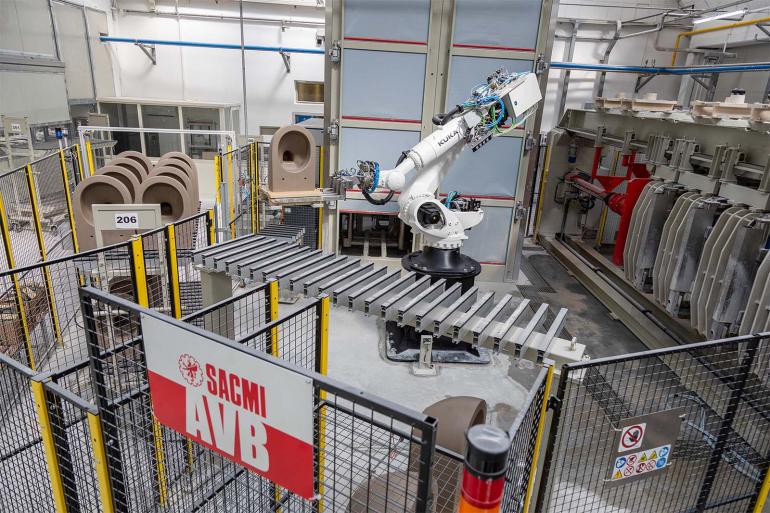
Finally, GSI has installed two new Sacmi AVM casting solutions for the production of complex WCs at its factory in Gallese (VT), bringing the number of pressure casting solutions adopted in recent years to 14, including ADM and ADS machines for washbasins and shower trays. The new investment is part of the company’s plan to fully automate its factory by reducing manual processing (e.g. by automating green piece finishing) and implementing advanced tracking, monitoring and control functions for the casting, glazing and handling lines. All information can be processed by the factory supervisor, allowing for real-time monitoring of KPIs including order management, times/quantities for items that have transited through the various stages and automatic alarm management.
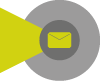
Did you find this article useful?
Join the CWW community to receive the most important news from the global ceramic industry every two weeks