Id-Tiles, for authentic Italian-made slabs
SACMI has introduced a new application that generates a digital identity card for products, effectively serving as a “protected designation of origin” label and offering benefits in terms of process control.
Quality is paramount in ceramic slab production. Sacmi’s Id-Tiles application assigns each slab a “digital identity card” containing detailed information about its characteristics throughout production, storage and sale, thereby optimising intralogistics.
Launched by Sacmi at Tecna 2024 in Rimini, the application is a module belonging to the HERE suite, a ceramic plant monitoring and management software capable of connecting machines and devices on the line with the factory ERP. Sacmi has further enhanced this software by developing dedicated packages tailored to specific objectives.
The main function of Id-Tiles is to perform digital tracking of the slab through every stage in the production process. The tracking technology begins by printing a unique code on each slab, normally immediately after forming but in some cases after the firing stage. Checkpoints along the production line collect data on the slab and add relevant information to its digital identity card on the HERE platform.
For example, when the code is written on the slab immediately after the forming stage, the system can integrate data from the vision system and record initial specifications such as quality and geometric and dimensional characteristics.
Additional data are collected at each subsequent stage (forming, digital decoration, firing) and instantly integrated into the system. This allows production managers to monitor the status of each slab in real time and access the information remotely if needed.
The system is modular and adaptable to the specific plant layout or monitoring requirements. A key feature of the application is its ability to communicate directly with production line machines, allowing it to automatically collect data. During the firing stage, for example, the kiln receives the slab ID, then monitors the slab’s parameters and provides precise information that is recorded on the HERE dashboard. These data can also be used to make real-time adjustments to the kiln in the event of deviations from the set parameters.
In addition to storing data generated automatically by the machines and standard controls, Id-Tiles allows for manual input of information such as colour coordinates, ensuring maximum adaptability to specific tracking or data recording needs.
Although one of the key advantages of Id-Tiles is its ability to optimise plant and warehouse management, leading European ceramic companies are also showing strong interest in its role as a “designation of origin” label. With Id-Tiles, disputes can be resolved objectively and effectively, even after many years. The system’s complete product traceability allows for precise tracking of processing operations, not only for entire batches but for each individual slab that has passed through the plant and warehouse.
Digital tracking also supports advanced logistics functions. The slab’s digital identity facilitates automated handling and storage management, optimising picking processes and streamlining handling and the composition of multi-item orders.
Process data management applications
Id-Tiles is just one of several new applications launched by Sacmi in recent months to manage process data, delivering immediate benefits in terms of line management, quality control and the optimisation of entire stages or departments.
Another innovation is the new Smart Powder Plant Control Room, an application that allows the body preparation department to be managed from a single location. The application receives raw material and formulation data directly from the ERP, allowing operations to be centralised. In keeping with the HERE system’s logic, its functions can be accessed remotely via PCs, tablets, smartphones or monitors placed at strategic points within the plant.
The same approach extends to the new line controllers designed specifically for the integrated management of finishing and decoration lines. These controllers allow line managers to oversee groups of machines or sequences of processes (such as squaring and grinding, lapping and finishing, and glazing/decorating lines), viewing and managing the entire line as if it were a single machine. This setup simplifies operations and enhances overall management and control.
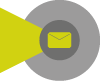
Did you find this article useful?
Join the CWW community to receive the most important news from the global ceramic industry every two weeks