Siti - B&T Group sanitaryware
o cater for the market requirements for high productivity and efficiency, Siti - B&T Group has developed two types of kilns for firing sanitaryware: the first is a shuttle kiln with innovative characteristics capable of firing and refiring sanitaryware articles of considerable size and highly complex shapes; the second HP continuous tunnel kiln is essentially suitable for high levels of production upward of 700-800 pieces/day.
The Astra shuttle kiln is able to solve all problems relating to thermal stresses generated in the piece during the firing cycle. Its burners have a very wide range of settings (5,000-250,000 kcal/h) and allow the temperature of the combustion gases to be regulated by mixing them with the ambient air. Temperature uniformity inside the kiln is essential for effective firing and this is guaranteed by the turbulence of the air supplied to the burners in a variable quantity and pulsing mode during both heating and cooling.
This kiln is entirely prefabricated and adapts perfectly for firing different types of products. Its insulation consists of ceramic fibre clad with plates of cordieritic/mullitic material anchored to the structure and can be equipped with one or two manual or automatic doors. Special attention has been focused on the combustion plant equipped with high velocity burners fed by two independent air supplies.
This system can also be used to introduce hot combustion gases into the kiln at a temperature of between 100/150°C so that they additionally act as a dryer. Each burner is equipped with automatic ignition, regulation and control systems. Temperature control is performed using thermocouples installed in the kiln. Adjustment and measurement of the combustion air and gas are performed by means of 4 sophisticated flow meters/transmitters. This system allows the supervision computer to control and automatically and instantaneously adjust the air-to-gas ratio of the volumes entering the kiln.
The HP tunnel kiln on the other hand is extremely flexible and can use natural gas, LPG, gas oil, kerosene or producer gas as fuel. The burners have automatic ignition and flame detection features. Consumption is low, in the region of between 1000 and 1300 kcal/kg of unfired product, depending on the cycle, the load and the type of material to be fired.
Due to the large number of burners (8 per module) and settings, the temperature variations are kept within ± 5-7°C according to the width of the kiln, ideal for firing any type of white or coloured material. The kiln adjustment system is of the fixed air and modulated gas type. Simple and economic, it is particularly suitable for this type of kiln which is essentially stable and consistent in its operation. A system for recovering the hot air from the cooling flue can be installed to feed the burners and thus further lower consumption by approximately 5%. The kiln is generally installed together with a pre-kiln for eliminating residual moisture from the material to be fired.
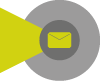
Did you find this article useful?
Join the CWW community to receive the most important news from the global ceramic industry every two weeks