Successful partnerships: the Gold Art and BMR experience
The partnership between Gold Art and BMR is an example of a virtuous collaboration that continues today with a focus on innovation and the future and an increasingly customised approach.
Gold Art (Pavullo, Modena, Italy) ranks as one of the leading international players in the segment of large ceramic slabs, which it produces in a range of modular sizes and thicknesses. With more than 30 years of experience, it is strongly focused on research and innovation, environmental sustainability and reduced energy consumption. Thanks to collaboration with leading suppliers, it now has a highly optimised production process and a high degree of flexibility that enables it to respond to the demands of its market with the utmost attention to detail. As Gold Art CEO Riccardo Monti explains, the market is changing very rapidly with a strong focus on logistics efficiency, which is now essential in the ceramic industry. This is particularly true for companies like Gold Art that have chosen to focus on make-to-order manufacturing with the production of a semi-finished product that is subsequently cut into sub-sizes.
One of Gold Art’s most virtuous collaborations began in 2015 with BMR, which was involved in the restructuring programme aimed at producing medium-large and large sizes with rectification and submultiple cutting. The partnership has continued over the years. In 2018, for the new plant devoted to the production of slabs and submultiples, BMR supplied three squaring and dry cutting lines and a slab lapping line consisting of two Leviga1600/12A Maxi machines, an acid treatment with two satellite applicators and two brushing machines (model Brush 3T SAT 1600 Brandeg.), all suitable for working with slabs up to 1600x3200 mm in size. A 12-head Supershine polishing machine, again for a maximum size of 1600x3200 mm, was installed and started up the following year.
Gold Art’s most recent investment consists of three squaring lines installed alongside the two existing lines. All three feature transversal and horizontal cutting for maximum flexibility and efficiency without wasting time or money. At the same time, a lapping and treatment line for the largest 1200x2800 mm size has been installed and started up, comprising two pre-grinding modules with 6 motors per side, two 16-head Leviga 1200 units, one 16-head Supershine machine and one 3-head Brush 1200 unit.
“The partnership with BMR has proved instrumental in enabling us to implement a radical change based on a new corporate mentality aimed at enhancing the value of finished products through an improved production process,” said Riccardo Monti. “Our trust in BMR has grown over the years in step with the constant investments and technological upgrades it proposes. It is always attentive to combine a high-quality product and service with consulting on the complete process. BMR have understood our need for innovation and in turn we have appreciated the more advanced aspects of their systems and taken full advantage of their technology. This has enabled us to achieve an optimised and efficient production process in which the high level of flexibility allows us to meet the needs of modular sizes and thicknesses. Added to this is the advantage of using a green-oriented technology that protects the environment while saving energy and money.”
Lapping and finishing in the large slab production facility
The finishing plant built between 2018 and 2019 for the large slab facility in Pavullo delivers a 20% increase in productivity, divided between around 12,000 sqm/day of porcelain tiles in a 120x120 cm size and 6,000 sqm/day of large slabs.
The first machine to be installed there was a squaring line for sizes up to 1200x1800 mm with transversal and longitudinal cutting and splitting, followed by a second line.
According to Antonio Bellei, Industrial Technical Director at Gold Art, “BMR has brought a clear improvement in ceramic tile quality with its technologies, making what was considered a finished product even better in terms of uniformity and calibre, while at the same time also improving warehouse organisation”.
Antonio Bellei also confirms the benefits of using SuperShine technology:
“SuperShine is a polishing machine that improves the line’s speed and the quality of the finish while cutting production costs and increasing product quality. It has evolved over the years with the introduction of new finishing solutions capable of ensuring an effective, consistent and high-performance workflow. As well as enhancing productivity by removing imperfections, the machine is also equipped with dry polishing technology that distributes the dry treatment and forces it into the surface pores, thereby acting as a super polishing machine. Its operating process is based on the mechanical, physical and thermal interaction between the tool, the surface and the applied chemical product and is designed to enhance the digital graphics of the tile and give the surface a high gloss finish and high degree of protection.”
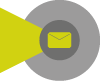
Did you find this article useful?
Join the CWW community to receive the most important news from the global ceramic industry every two weeks