Laminam set to revolutionise sustainability in the field of large-size surfaces
The company is launching the revolutionary twO by Laminam surfaces as part of its commitment to economic, environmental and social sustainability.
Despite the global economic downturn, a forecast 4.5% contraction in residential building worldwide and a consequent decline in ceramic tile consumption, the Laminam group of Fiorano Modenese achieved positive results in 2023, underscoring the group’s capacity to thrive in even the most challenging circumstances. As Chairman and CEO Alberto Selmi pointed out during the presentation of the 5th Sustainability Report, the group successfully navigated a deteriorating competitive landscape and decline in profitability caused by the surge of new Asian competitors offering low-priced products in the international ceramic tile markets.
Economic performance
Despite these challenges, the Italian ceramic group, a leader in the large surface segment, continued to outperform the Italian ceramic industry as a whole, which on average experienced an 18% decline in volume sales and a 14% decrease in total turnover.
Laminam Group’s consolidated revenue in FY 2023 was €237.4 million, a fall of just 2% compared to the €243.3 million of 2022 (or 1.6% growth on a constant EUR/RUB exchange rate basis). This represented an 85% growth in revenue compared to 2019 (the last pre-Covid year), with a 2020-2023 CAGR of +23%. EBITDA stood at 11 % of consolidated revenue.
In volume terms, sales remained effectively stable at 2022 levels (+0.1 %), up 50% on 2019.
Sales in Italy (+6%) and above all in European markets (+15%) made a positive contribution to turnover, while sales to geographical areas outside Europe declined. Overall, exports accounted for 77% of total revenues.
Towards the (renewable) electrification of the industrial process
Environmental sustainability continues to be a strategic focus for Laminam. In 2023, the company invested in reducing its reliance on traditional energy sources, improving efficiency in consumption (primarily energy and water use) and preserving biodiversity. In one particularly notable initiative, Laminam completed a large-scale project to expand and revamp the photovoltaic array at the Fiorano Modenese factory, which will be complemented by further new photovoltaic systems planned for the site in Borgotaro (Parma). Additional efforts include the development of an innovative trigeneration process and the progressive electrification of the industrial cycle.
Self-produced energy from photovoltaic arrays grew significantly compared to 2022 (+62%), while renewable electricity drawn from the grid increased by 15.3%. The ratio of natural gas to electricity also decreased, with gas accounting for 76% of total energy consumption (compared to 79% in 2022) and electricity the remaining 24%.
The company also continued its decarbonisation efforts, including R&D focused on developing new low-temperature body mixes and exploring the use of waste materials from other industries within these body mixes.
At the two Italian factories, the volume of treated and reused wastewater reached 33,563 m3. The proportion of recycled water within total water usage consequently increased from 50.4% in 2022 to 51.3% in 2023.
In terms of welfare policies, the company has introduced new initiatives aimed at improving work-life balance and has implemented specific workplace safety measures that have contributed to a steady reduction in accident rates.
2024 environmental targets
The group currently has several projects in progress. At the Fiorano site, plans are in place to construct a fifth photovoltaic array with a capacity of about 600 kW. Preliminary work for this installation was completed in 2023. This will bring the total installed power at the site to approximately 2,000 kW, with an expected annual production of 2,400 MWh. Additionally, the installation of the first 516 kW photovoltaic plant at the Borgotaro site is nearing completion.
Three of the four kilns installed at the Fiorano site are hybrid, capable of consuming 70% less gas than traditional kilns. An engineering study conducted in 2023 to explore the feasibility of expanding the water treatment plant at the same site has been approved for 2024. This expansion aims to recover about 30% of industrial water for internal use and consequently reduce transport traffic. Projects are also underway at both sites to recover pressing filter sludge.
Technological innovation
Laminam’s Technological Laboratory carried out several projects during the year. The first involved the formulation of a roller engobe aimed at preventing corrosion of the slab surfaces, thereby avoiding the problem of alkaline attack following storage of the slabs outdoors and in humid environments.
The second project involved developing an innovative formulation as an alternative to absolute white body mix in the production of white slabs.
In 2023, the Technological Laboratory continued its research into a new ceramic body mix that can be fired at below-standard temperatures. This study is particularly significant in terms of reducing the environmental impact of ceramic products in relation to CO2 emissions and offers substantial benefits in terms of energy consumption.
A study and design patent has also been filed with the aim of improving environmental performance through CO2 capture using broad-spectrum filtration (end-of-pipe process of thermal condensation and CO2 abatement in ceramic production). Tests have confirmed the efficacy of this process, and Laminam’s technicians are now focused on stabilising CO2 in a crystalline form.
Research is also continuing into a new electric spray dryer (also patented), which will increase efficiency and reduce environmental impact.
Product innovation: launch of the first 2 mm thick ceramic surface
twO by Laminam is the Italian brand’s latest initiative aimed at revolutionising the world of ceramic surfaces for construction and furnishing.
The thinnest and lightest material ever produced in the ceramic industry, it is both innovative and sustainable and maintains the renowned technical and aesthetic performance of Laminam products despite its minimal thickness of just 2 mm. This breakthrough expands the potential uses of ceramic materials and opens up new market areas.
Production of the patent-pending twO by Laminam surfaces requires numerous changes compared to the methods and processes normally used by the company. These involve areas ranging from the body mix to the spray-dried powder, from pressing to internal transport, and from more rapid firing in electric kilns to gluing, packaging and logistics. At the same time, the surfaces have an extremely low environmental impact over their entire life cycle as the use of less material equates with reduced energy and water consumption and less waste

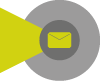
Did you find this article useful?
Join the CWW community to receive the most important news from the global ceramic industry every two weeks