Sanindusa opens the way to the digital r-evolution in the sanitaryware sector
With the recent installation of a new generation plant supervisor at the Tocha factory, Sanindusa’s ambitious modernization plan, started in 2019, has been completed.
Sanindusa, an important Portuguese sanitaryware manufacturer, has recently completed, together with Sacmi, its ambitious plant renovation project at is production site in Tocha. A completely new production plant, now equipped with Sacmi’S HERE supervisor, opening the way to the digital r-evolution in the sanitaryware sector.
The HERE plant supervisor is an integration both to the substantial fleet of Sacmi machines installed at Sanindusa – pressure casting machines, AGV, robotized glazing systems – and to all the other technological and plant solutions available at the factory.
Modular and scalable, HERE is configured as the first platform on the market specifically designed to meet the requirements of the ceramic work process, thanks to its ability to manage integrated data and production processes from raw materials up to shipments and the finished product. Thanks to HERE’s advanced functions as well as the sensors installed on the machines – the software is completely integrated with the control boards for automation of the cells – it is possible to monitor the operating state of the plant, keep the Key Performance Indicators (KPI) under control and, above all, react to the feedback received by, for example, managing any deviations in production in real time and scheduling maintenance jobs.
The distinctive feature of HERE is its high level of modularity meaning it can be easily adapted to the needs of the customer. Scalable over time, HERE can be integrated with new functions according to new requirements and the latest advances towards factory digitalization. In the case of Sanindusa, one of the most important requirements was to control the status of the semi-finished piece storage area in real time i.e. the number of pieces stored post-casting during ageing, number of pieces being dried or glazed.
This is why the HERE supervisor has been integrated with the LGV handling system to allow for full control of these functions. Alongside this, is the tracking module, specifically developed to display the current stock status, with an indication of the pieces loaded on every car, their number, type and model as well as “parking” time elapsed.
Among the advantages of monitoring the pieces in this way, achieved thanks to the bar code tracking system integrated at every position along the line, is the possibility to generate statistics reports, of particular importance during the sorting stage, to associate any defects identified in certain areas of the piece with the related corrective actions which can be quickly activated on the plant. All this improves quality, reduces waste and leads to an increase of first grade product.
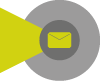
Did you find this article useful?
Join the CWW community to receive the most important news from the global ceramic industry every two weeks