Toshiba TEC CF1 family of industrial inkjet heads
Over 40% of ceramic tile manufacturers have already switched to digital inkjet decoration. Just as Dyson's cyclone concept revolutionised the vacuum cleaner industry, it was a radically new print head design feature that allowed inkjet systems to be used successfully within the extremely harsh environment of ceramic tile production lines: "through-channel fluid recirculation".
Through-channel fluid recirculation in Toshiba TEC industrial inkjet heads continuously moves the large pigment particles carried by high-viscosity fluids across "side-shooting" inkjet head nozzle openings. This constant flow prevents particle sedimentation and the accumulation of air bubbles that would lead to unreliable jetting and nozzle blockages. It also allows fluid temperatures and viscosities to be accurately controlled by an in-circuit, fluid-conditioning unit.
Toshiba TEC research has shown that the flow rate required for through-channel fluid recirculation to be reliably effective is around 100ml / minute for each 100mm of colour bar width. So in a 700mm wide, multiple head colour bar assembly, the total flow rate needs to be around 700ml / minute. This flow must be directly across the nozzle openings to prevent sedimentation.
Where the flow rate in other implementations of fluid recirculation is too low (some offer only 10ml / minute or less) or where the flow is not directly across the nozzle openings (some designs position the flow channels millimetres or even centimetres from nozzle openings), these systems will have minimal effect in preventing particle sedimentation.
Single-pass printing of up to 8 colours is now standard in ceramic applications. While this is high compared with other industries, fewer grey levels per colour are required: it's normally sufficient for inkjet nozzles to produce 3 different droplet sizes (4 grey levels). A reduction in the number of grey levels allows print speeds to increase. Ceramic tile production lines generally run at up to 25m / minute, although in a few countries including Brazil, some lines run at 40-50m / minute, presenting further challenges for inkjet head manufacturers.
The Toshiba TEC CF1 family of industrial inkjet heads is ideally suited to ceramic applications, catering for large drop volumes and high viscosities. CF1 family heads offer highly accurate dot placement and consistent print densities across single and multiple heads. And a monthly production of 5-figure quantities of industrial inkjet heads enables Toshiba TEC to keep its prices at very competitive levels.
Having overcome all barriers to inkjet decoration for ceramics, head and press manufacturers are now seeking new applications in the ceramics industry. The focus is on special effects, such as textures, metal effects, and various special finishes. The use of oil-based carriers for these additional effects layers would mean a significant increase in pollution during the firing cycle, so there will have to be a shift towards water-based inks.
Toshiba TEC will continue to innovate in this area.
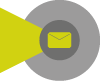
Hai trovato utile questo articolo?
Unisciti alla community di CWW per ricevere ogni 15 giorni le principali novità da tutto il mondo sul settore ceramico