The Easy Factory. SACMI presents at Tecna its project for a new ceramic industry
On show at Tecna in Hall B1, the SACMI ‘easy factory’ balances environment-friendliness, productivity and quality flawlessly.
Productivity, control and eco-friendly design are the three guiding principles behind Sacmi’s new “easy factory” concept showcased at Tecna 2024, the international exhibition of technologies and supplies for surfaces (Rimini Expo Centre, 24-27 September). As always, Sacmi will welcome visitors to Booth B1, where they can view machinery and watch live demos for the entire duration of the show.
Sacmi’s “easy factory” concept combines powerful, high-performance machines with automation and digital controls throughout the entire production process, from body preparation to logistics. It also incorporates innovative thermal processes that support the industry’s climate-neutral goals. This approach achieves a perfect balance between environmental sustainability, productivity and high quality, freeing up resources for increasingly ambitious projects.
A zero-emissions factory
Sacmi’s revolution in thermal process control begins with the kiln. The first company in the world to develop a 100% hydrogen kiln, Sacmi is now presenting its new 100% electric kiln prototype exclusively at Tecna 2024.
As part of its efforts to build a “zero-emissions” factory, Sacmi is introducing its new hybrid concept spray dryers and dryers. These patented solutions are already available on the market and are designed to enable customers to optimise their investments in renewable energy sources and ensure smooth operation under all production conditions.
One such machine on display at Tecna is the innovative 7-tier dryer module, newly engineered to maximise operational flexibility, enhance process control and reduce maintenance.
A powerful and highly productive factory
The aim of Sacmi’s plant engineering efforts is to raise performance to new levels while reducing consumption and streamlining management.
For the forming stage, Sacmi is presenting the new high-productivity PCR model machines from the Continua+ family. With productivity rates as high as 12 linear metres per minute, these machines can achieve outputs of more than 30,000 sqm per day and widths even up to 200 cm fired, while maintaining the highest levels of efficiency in the market (specific consumption of just 0.04 kWh/sqm during compaction). They generate very low levels of waste regardless of product size, with the potential to recycle all waste back into the process. Furthermore, they require more than 90% less hydraulic oil compared to conventional or discontinuous presses.
Easy to control, powerful performance
The highlight of the sorting line is the new packaging machine model, which visitors to Tecna will have the opportunity to see as absolute preview. The new D-Roll, which complements Sacmi’s Dinamica Line, stands out for its market-leading productivity (it is capable of handling 13 packs per minute of 60x60 cm size tiles) and exceptional operating autonomy, allowing entire work shifts to be performed without an operator. Visitors to the show will have the opportunity to see the machine operate in conjunction with a new D-P&P gantry palletizer (complete with a smart picking gripper) and with Spinner, Sacmi’s revolutionary 100% electric multi-wheel automatic vehicle designed to manoeuvre through tight spaces.
An automated, digital and connected factory
At Tecna, Sacmi is showcasing a cutting-edge machining and finishing control solution that uses exclusive BMR technology. This creates a unique factory environment where human-machine interaction is simple and intuitive thanks to the seamless integration of mechatronics, vision systems and AI. The use of digital and vision controls optimises tool consumption.
Additionally, Sacmi is presenting the Squadra Dry Vision Plus dry squaring machine, a new system designed to combine operational flexibility and control with significantly reduced noise levels and exceptional ergonomics. Also featured is LeviCompact, an innovative BMR patented solution that delivers greater speed and uniformity compared to traditional machining thanks to the use of two 10-head parallel tilting bridges which reduce floor space requirements by up to 45%.
Visitors will also have a chance to see Italvision’s range of inspection systems which ensure 100% digitalised quality control, resulting in zero waste and zero additional costs. This technology significantly reduces defects and enhances quality, transforming the factory into an intelligent workspace where machine vision plays an important part in process control.
Another major new product on display is OneVision, the advanced self-learning unfired material inspection system that increases overall quality while reducing defects and associated costs and is capable of adapting to different production scenarios. The Deep Digital decoration line is complemented by a number of new solutions, including the Line UP optical synchro-aligner designed for optimal management of complex decoration lines and multiple machines in sequence; the Decoration Line Manager system which ensures integrated control; and Optima DHD which checks for defects and provides feedback for the main DHD operating parameters.
Moving downstream from the kiln, Sacmi is presenting Flawmaster+, a machine designed for rapid, simple and reliable defect detection on ceramic surfaces, as well as the latest-generation OPTIMA Kiln camera inspection technology. This solution is designed to keep pace with the digital evolution of Sacmi kilns by combining precise and accurate control of colour, flatness, dimensions and defects with the capability to perform real-time feedback control on the kiln’s parameters.
The Sacmi digital factory ensures greater process control and fewer unexpected events. It includes the new HERE suite modules, such as the body preparation control room and ID-Tiles tracking system, which creates a kind of identity card for each individual tile and keeps track of all products as they pass through the various process stages. In addition, new line controllers are used to improve and streamline all individual process stages, such as digital decoration and processing downstream from the kiln (BMR lapping, squaring and finishing lines), to create unique and infinitely repeatable products.
Sacmi is also upgrading its customer service with the introduction of new digital tools, which along with the well-established Smart Service plans are capable of improving performance with data-driven decisions. The integration of IoT technology allows for in-Cloud sharing of machine operating data, shifting maintenance strategies towards predictive logic.
Logistics automation
With SacmiCassioli Intralogistics and digital tracking, Sacmi is able to deliver a fully automated plant logistics offering complete with highly customisable and dedicated solutions for the ceramic industry.
This high level of automation actually shifts the focus of the production process back to human operators by easing their workload and simplifying management despite the greater overall complexity of the system, at the same time improving the overall factory environment.
Designed to be increasingly clean and quiet, the Sacmi factory aims to achieve a perfect balance between human and machine resources, improving competitiveness while meeting the growing need to reduce the impact of processes on the environment, people and communities.
Sanitaryware and tableware: changing the approach to factory management
In keeping with the global industry trend led by Sacmi for many years, sustainability and automation are central to Sacmi’s Sanitaryware & Tableware range on display at Tecna.
The tagline for this event-within-an-event organised by the Sanitaryware & Tableware division is “Explore our solutions to create your perfect mosaic”. This is because the range consists of a series of individual solutions that customers can assemble like a mosaic to improve plant automation and digitalisation while maintaining a strong focus on circularity.
For example, the ultrafiltration solutions offered can reduce the plant’s water requirements by more than 80%, allowing waste water and materials to be fully recycled and used as resources. With robotised finishing of both greenware (inside the casting cells) and whiteware, increased automation goes hand in hand with higher quality work and a cleaner factory environment.
Here too, Sacmi’s key strength is its high level of configurability, enabling the company to work closely with customers to achieve automation and productivity goals within the framework of the circular economy.
Open week at Sacmi
During Tecna, Sacmi will as usual be organising presentations and dedicated events at its own facilities , giving visitors a unique opportunity to experience some of the most innovative solutions first-hand.
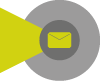
Did you find this article useful?
Join the CWW community to receive the most important news from the global ceramic industry every two weeks