Keracromia®, ottimizzazione della produzione digitale
La tecnologia digitale sta assumendo sempre maggiore rilevanza per l’industria ceramica italiana. Volutamente usiamo il termine “tecnologia” e non “stampa” digitale, perché troppo spesso si considera centrale la stampante, trascurando o sottovalutando i passi che portano dall’idea grafica all’operazione fisica.
Altrettanto spesso, si utilizzano tecniche ed esperienze mutuate da settori differenti che non tengono conto delle specificità della produzione ceramica, magari pretendendo di lavorare con gli stessi strumenti e le stesse metodologie usate nel processo serigrafico tradizionale.
Al contrario, il sistema Keracromia® propone un approccio completamente digitale e oggettivo, progettato sulle caratteristiche della produzione di piastrelle ceramiche, fornendo strumenti, procedure e metodologie di color management da un lato, di analisi e controllo del processo di stampa digitale dall’altro, con l’obiettivo di rendere il prodotto ceramico all’avanguardia della ricerca estetica e tecnica, oltre che economicamente competitivo.
Indipendente dai produttori di materie prime, di macchine e dagli studi grafici, il sistema si adatta a qualunque scelta tecnologica adottata dalle aziende ceramiche, supportando tutti i fornitori di stampanti e di inchiostri ceramici per inkjet.
Grazie alla flessibilità del sistema, Keracromia® ha dimostrato di adattarsi con facilità alle esigenze produttive di aziende ceramiche di ogni dimensione, dalle medio-piccole ai Gruppi multinazionali, con organizzazioni e strategie produttive e commerciali molto diverse.
I risultati
L’aspetto fondamentale della produzione di piastrelle ceramiche è la sintesi tra qualità percepita, rapidità di risposta alle richieste di mercato e costo, perseguita attraverso:
- L’ottimizzazione dei tempi necessari per passare dall’idea grafica al prodotto
- La costanza di risultato e la riduzione delle difettosità
- Il miglior utilizzo degli impianti
- La riduzione delle materie prime impiegate.
Ottimizzazione dei costi: gli inchiostri
I costi possono essere direttamente misurabili, oppure nascosti nelle pieghe di una diffusa inefficienza delle varie aree progettuali e produttive.
Gli inchiostri fanno parte della prima specie e costituiscono una percentuale importante del costo di prodotto. La loro ottimizzazione si ottiene con l’utilizzo di tecniche colorimetriche digitali. Come è noto, maggiore è il numero di tinte base, maggiore è il numero di combinazioni per raggiungere un determinato colore. Grazie alla possibilità di gestire un numero virtualmente infinito di differenti tinte, Keracromia® consente di scegliere la combinazione ottimale. Un esempio significativo riguarda un’azienda ceramica italiana che, nel passaggio da stampanti a 4 barre colore alle attuali stampanti con 8 barre colore, ha ottenuto un risparmio del costo globale degli inchiostri superiore al 50%.
Purtroppo invece non sono rari i casi in cui, per la limitazione degli strumenti utilizzati, per una valutazione economica miope o per una conoscenza non approfondita delle tecniche digitali, si usano solo 3 tinte anche nelle macchine che ne hanno a disposizione un numero superiore.
Scegliere automaticamente la migliore ricetta significa anche poter cambiare tinte e/o fornitore in funzione della convenienza economica, senza necessità di trasformare manualmente le grafiche, avventura costosa e dall’esito incerto.
Miglioramento della qualità
Migliorare la qualità è un altro modo di ottimizzare i costi, sia riducendo gli scarti, sia mantenendo stabile il tono e i toni a magazzino. Keracromia® offre strumenti per la verifica della qualità e della costanza della stampa, indipendentemente dal fornitore e dalla configurazione del dispositivo fisico, in particolare l’allineamento delle teste e delle barre e la linearità di deposizione degli inchiostri.
Migliore utilizzo degli impianti
È un aspetto fondamentale anche se più difficile da misurare, che riguarda sia l’aspetto pre-produttivo, ovvero quando si passa dall’idea grafica alle attrezzature della macchina digitale, sia quello direttamente legato alla realizzazione. Nella fase di messa a punto, Keracromia® riduce drasticamente i tempi e i costi, sostituendo alla realizzazione fisica di staffette e al loro controllo visuale, la verifica virtuale direttamente sui dati forniti dal PC. Questo consente di raggiungere il risultato ottimale per un particolare prodotto su uno specifico processo già al primo tentativo. In fase di produzione invece, la verifica virtuale di Keracromia® effettuata in parallelo tra molti modelli di processo, offre la possibilità di scegliere rapidamente quale sia la migliore linea produttiva per uno specifico lotto.
Gli strumenti di Keracromia®
Gli strumenti di Keracromia® sono unicamente digitali e completamente basati su numeri, ossia una grandezza oggettiva e universale: non si usano monitor tarati, cabine luce, confronti visuali, né all'operatore è richiesto di prendere una sola decisione basata sul suo giudizio soggettivo.
Keracromia® impiega uno scanner spettrale in varie versioni (per piastrelle, pietre, legni ed altri materiali), con dimensioni fino a 900x1600 mm e con spessori fino a 70 mm., completamente motorizzato sui tre assi e con risoluzione fino a 720 punti per millimetro
Al posto di target progettati per la stampa su carta, si impiegano tavolozze specifiche con migliaia di combinazioni di tonalità sulla base delle caratteristiche di stampa (numero di barre, capacità di scarico).
Le tavolozze sono realizzate fisicamente con il processo produttivo che si vuole modellare, acquisite con lo scanner spettrale ed elaborate con il Modulo che crea il modello matematico dello specifico processo produttivo
Il Modulo di separazione mette poi in relazione il file grafico che si vuole realizzare con il modello del processo (o anche, in contemporanea, con più modelli alternativi) per creare una "staffetta virtuale" e fornire una valutazione numerica di quanto differisca il prodotto realizzabile da quello ipotizzato e quale sia il miglior processo utilizzabile.
Il file grafico può essere già esistente e scaricabile tramite web, oppure da acquisire: in questo caso l'opzione fortemente suggerita è lo scanner spettrale, ma la flessibilità del sistema permette l'utilizzo di altre sorgenti non spettrali, come scanner RGB, dorsi digitali o altro.
Il risultato dell'elaborazione è mostrato nelle figure in basso: la prima mostra l'immagine originale, a seguire la "staffetta virtuale" che evidenzia il grado di somiglianza e le aree che il processo non riesce a riprodurre. Il risultato mostra ad esempio che, fissato un certo limite di errore, la perfetta realizzabilità è di oltre il 92% della superficie, mettendo in evidenza le aree in cui esiste una difformità.
Il pannello di controllo permette all'operatore di variare l'errore accettabile e di mascherare o evidenziare le aree difformi: ovviamente, più grande è l'errore ammesso, minori le aree difformi.
Se il risultato è accettabile si può proseguire con la generazione delle attrezzature, oppure si può decidere di abbassare la soglia o scegliere un diverso processo produttivo avente la capacità di generare un insieme più ampio di colori.
Tutto questo senza costi e in tempi estremamente ridotti, per l'utilizzo della verifica virtuale di Keracromia® e non di staffette fisiche.
Nel caso invece fosse necessario intervenire sulla grafica, Keracromia® mette a disposizione dell'operatore le informazioni necessarie alla rapida ed efficace modifica, per procedere poi alla successiva nuova verifica virtuale.
Le caratteristiche e il funzionamento di Keracromia® sono verificabili presso KeraLab, il service creato da Macs Tech e Officine SMAC a Fiorano Modenese.
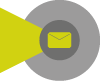
Hai trovato utile questo articolo?
Unisciti alla community di CWW per ricevere ogni 15 giorni le principali novità da tutto il mondo sul settore ceramico